Manufacturers have developed refrigerants specifically designed for commercial and industrial refrigeration, emphasising maximising performance in supermarket applications. These refrigerants have low global warming potential, aiming to minimise their impact on climate change.
In the realm of air conditioning systems, there have been notable advancements in developing high-efficiency models. These advanced systems incorporate variable-speed compressors and fans and responsive controls that can adapt to various temperature conditions. Notably, many of these systems also double as heat pumps, allowing cooling and heating capabilities. The available size options for these systems have expanded significantly, catering to various applications, from compact mini splits to large multi-ton units exceeding 100 tons. Major manufacturers are increasingly embracing the trend of offering high-efficiency heat pumps.
One significant development in air conditioning systems is the integration of sensor technologies and remote monitoring capabilities. Modern heating and cooling systems now have built-in temperature and humidity sensors, contributing to enhanced energy efficiency and optimal comfort. The decreasing cost of pressure, temperature, and refrigerant leak detection technologies has led to their widespread integration into equipment. Consequently, much sensor data is now accessible to energy management systems.
The diverse selection of independent measurement and recording devices facilitates remote monitoring, utilising Bluetooth, Wi-Fi, or cellular signals to track space, environmental conditions, and electrical power consumption.
Environmental concerns
In line with growing environmental concerns, manufacturers have introduced environmentally friendly refrigerants with low global warming potential (GWP), mainly designed for commercial and industrial refrigeration. Supermarkets have been a focus for optimising the performance of these refrigerants. CO2-based central systems are rising, while stand-alone refrigeration units, whether air-cooled or water-cooled, employ hydrocarbons with very low GWP.
To further enhance efficiency, stand-alone systems can be connected to a central hydronic loop, enabling individual equipment with varying loads to operate at maximum efficiency. This setup also allows for the capture and utilisation of waste heat in other building areas. By considering the installation and testing of equipment, this approach minimises the required refrigeration capacity and refrigerant usage, thereby reducing the risk of leakage during installation and maintenance.
Advanced control technologies have revolutionised the diagnosis of issues in refrigeration systems, enabling technicians to conduct repairs more efficiently. This minimises equipment downtime, reducing the risk of food spoilage and occupant discomfort. With a clearer understanding of the problems, technicians can be dispatched to buildings more effectively.
Furthermore, reducing refrigerant lines decreases the chances of leakage and the need for extensive support. However, these enhanced capabilities necessitate updated training and certification for technicians. Numerous companies and industry associations provide specialised training programs to meet these new demands.
Remote sensor technology plays a crucial role in the transportation industry, with sensor manufacturers producing remote sensors linked to GPS. These sensors monitor the conditions of products, such as temperature and humidity, ensuring that they are maintained within appropriate ranges throughout the distribution process. Some sensors stay connected through cellular technologies, while others store data for future access.
The quest for improved refrigeration system efficiency, sensing, and controls continues, particularly in managing perishable goods. Various equipment configurations are available to minimise refrigerant usage and utilise hydronic loops for heat removal from the equipment. This approach leads to increased efficiency and reliability of the equipment.
Automated Fault Detection and Diagnostic (AFDD) systems are advancing in scope and effectiveness. These systems can be integrated within the equipment, building automation systems, or deployed throughout an entire enterprise. Comprehensive AFDD systems can identify faults and alert building operators and maintenance personnel about critical issues and performance deterioration. Some systems even enable technicians to diagnose and resolve system problems remotely.
The advancements outlined here demonstrate the ongoing commitment to developing high-efficiency air conditioning systems that prioritise energy efficiency, environmental sustainability, and operational effectiveness. These innovations promise to reduce energy consumption, minimise environmental impact, and ensure optimal comfort in various applications across industries.
References:
Analysis of Fault Data Collected from Automated Fault Detection and Diagnostic Products for Packaged Rooftop Units; NREL/TP-5500-77077
Shoukas, Gregory; Bianchi, Marcus; Deru, Michael
Innovations in Sensors and Controls for Building Energy Management: Research and Development Opportunities Report for Emerging Technologies; NREL/TP-5500-75601
Sofos, M.; Deru, Michael; Gupta, E.; Benne, Kyle; Blum, D.; Bohn, T.; Fares, R.; Fernandez, N.; Fink, G.; Frank, Stephen; Gerbi, J.; Granderson, J.; Hoffmeyer, D.; Hong, T.; Jiron, A.; Johnson, S.; Katipamula, S.; Kuruganti, T.; Langevin, J.; Livingood, Bill; Muehleisen, R.; Neukomm, M.; Nubbe, V.; Phelan, P.; Piette, M.; Reyna, Janet; Roṭh, A.; Satre-Meloy, A.; Specian, M.; et al.
Contributed by:
Energy Efficiency and Renewable Energy
Department of Energy,
Washington DC.
Cookie Consent
We use cookies to personalize your experience. By continuing to visit this website you agree to our Terms & Conditions, Privacy Policy and Cookie Policy.
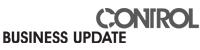