The management of temperature-sensitive goods within the cold chain industry presents unique challenges. Swarup Bose, Founder and CEO, Celcius Logistics discusses challenges and innovative solutions, including IoT-based systems and PCMs, aimed at ensuring the preservation of valuable products.
What are the types of products that require cold chain management, and what challenges are associated with their handling?
Cold chain logistics is pivotal in delivering essential and high-demand products, encompassing frozen foods, dairy products, fresh produce, meat, seafood, and pharmaceuticals. Within the pharmaceutical industry, the cold chain is vital for preserving and conveying essential items such as vaccines, intermediates, and high-value medications. These must be stored and transported under precise temperature conditions to maintain effectiveness.
Managing the cold chain presents many challenges, each contributing to the overall complexity of the process. First and foremost, the issue of unreliable power supply must be addressed. The inconsistent availability of electrical power wreaks havoc on the temperature control within the cold chain. Another significant challenge is the need for refrigeration facilities. This deficiency severely impacts the quality and safety of the products being transported.
Moreover, the absence of standardised temperature control measures and monitoring systems during transportation poses a substantial hurdle. This lack of uniformity compromises the quality and safety of the products in transit. The situation is reminiscent of attempting to cook without a recipe – achieving consistency becomes a formidable task. Infrastructure problems further exacerbate the complexity of cold chain management. Limited tracking technology, a shortage of specialised refrigerated vehicles, inexperienced drivers, and mishandling during delivery collectively create significant obstacles. This scenario is akin to trying to build a house with inadequate tools and an unskilled workforce – a recipe for many difficulties.
Lastly, the last-mile challenges present a unique set of issues, particularly in remote areas with limited connectivity and storage facilities. Maintaining the integrity of cold chain products becomes a formidable challenge in such environments. It’s like walking a tightrope without a safety net – high risk and the potential for significant losses are ever-present.
Addressing such issues effectively in India, significant investments are needed in enhancing cold storage infrastructure, speeding up the adoption and integration of technology, implementing advanced refrigeration technologies, and optimising logistics processes. These measures are essential to reduce losses and ensure a resilient cold supply chain in India.
How are sustainability and environmental concerns being managed in the context of cold chain logistics?
Our goal has been to create an uninterrupted cold supply chain by tackling the structural weaknesses within the cold supply chain industry, thus establishing an unparalleled digital ecosystem. We use innovative technology to enhance energy efficiency, minimise damage and losses, and incorporate more environmentally friendly practices wherever feasible. With the recently acquired funding, we intend to expedite technological advancements to address the fragmented nature of the cold supply chain, thereby reducing the waste of perishable goods. This will contribute to the development of a sustainable future.
How critical is maintaining a continuous cold chain in the pharmaceutical sector, especially when transporting vaccines and other temperature-sensitive medicines?
Storing and transporting temperature-sensitive items, particularly pharmaceuticals, can be quite challenging. Even minor temperature fluctuations can render the entire shipment unusable. We have leveraged tech-enabled innovations to ensure efficiency and real-time monitoring.
Through the use of technology-enabled and connected refrigerated vehicles for all our shipments, we guarantee that the ideal temperatures are consistently maintained throughout the entire journey. Irrespective of external environmental conditions, our cargo remains well-preserved in a stable and uniform temperature.
Some of these innovations encompass IoT-based Temperature Measurement Devices (TMDs), door sensors, temperature sensors, and GPS devices. It allows us to track and monitor the products throughout their journey. These devices provide continuous alerts and updates in case of temperature variations, facilitating the identification and resolution of any issues. Additionally, we also use Phase Change Material (PCM) for insulating the products. It efficiently absorbs heat from the surroundings to sustain the optimal temperature within the containers.
Even when stored in warehouses, each unit has a temperature sensor connected to an AI and IoT-based device that monitors the product’s temperature.
What are the recent innovations in refrigerants in the cold chain process?
The use of phase change materials (PCMs) in the Indian cold chain industry has become a recent and growing trend, especially since the pandemic. PCMs offer superior effectiveness in maintaining low temperatures by absorbing energy during phase transitions to supplement efficient cooling. Europe, at present, is the market leader for phase change materials, and an advanced PCM could potentially hit the market in 2026.
In India, several companies and domestic brands have taken it upon themselves to manufacture PCMs, aiming to support the cold chain industry. Increased investments in the cold chain and reefer sectors have also played a role in the swift adoption of PCMs. Considering these factors, in the coming years, the industry is likely to witness widespread adoption of phase change material.
How do the IoT and sensor-based systems improve the monitoring and management of temperature-sensitive products during their journey through the supply chain?
The cold chain industry has witnessed a rapid surge in technological integration in recent years. IoT-based thermal sensors, which oversee product temperatures during transportation and storage, have played a vital role in mitigating damage caused by human errors. These sensors issue alerts when temperature deviations occur, enabling swift resolution and reducing transit time.
Furthermore, technology has empowered us to establish a unified cold chain network that fosters seamless cooperation among various entities, ensuring full traceability, transparency, and accountability.
How can collaborative endeavours between cold chain providers, warehouses, and logistics firms improve the transportation of temperature-sensitive products?
A significant challenge in the cold chain industry is the need for more reefer trucks and warehouse storage facilities. Although there has been some improvement in the numbers in recent years, there is still significant potential for growth. In India, reefer trucks and storage facilities need help to meet market demands, and a major contributing factor to this issue is the fragmented distribution approach within the cold supply chain industry.
One of the most effective and cost-efficient solutions to address these infrastructure deficiencies is establishing a nationwide network that optimises utilising available resources. Currently, we are the sole cold chain aggregator platform in India, and our primary objective is to facilitate seamless collaboration within the industry. We also encourage transportation providers to enter the cold chain sector and provide financial and technological support to regional transporters, assisting them in meeting GDP (Good Distribution Practices) requirements.
What role does regulatory compliance play in the cold chain industry?
To safeguard the well-being and quality of temperature-sensitive goods, the cold chain sector adheres to stringent regulations and quality benchmarks. Regulatory authorities and industry associations have developed rules encompassing temperature management, handling protocols, documentation, and the maintenance of records. They are all aimed at preserving product quality and reducing the potential for contamination risks.
What initiatives should be considered for workforce training and skill development in cold chain operations and logistics?
Managing a technology-driven cold chain necessitates extensive involvement from on-site personnel, including individuals ranging from pickers and loaders to supervisors. Everyone must be integrated into the technological ecosystem. The handling of cold-sensitive products requires detailed oversight, and individuals must receive training to understand the consequences of mishandling items such as vaccines and temperature-sensitive goods. This awareness is essential in preventing wastage. Comprehensive training from entry-level employees to top executives is paramount when dealing with a delicate supply chain like the cold chain.
Cookie Consent
We use cookies to personalize your experience. By continuing to visit this website you agree to our Terms & Conditions, Privacy Policy and Cookie Policy.
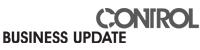