Energy is consumed by HVAC systems through a number of processes. Air is typically distributed through the ductwork via an electrically‐powered fan. Cooling coils remove heat from the air. Heating coils add heat to the air.
Through normal HVAC usage, particulate in the air slowly collects on the surfaces of various HVAC components, resulting in a gradual loss of energy efficiency. Some loss of efficiency via a single dirty component may be minor. When the loss through each component is added up, however, the impact could be considerable. Generally, the greater the build-up, the greater the energy loss.
Removal of the build-up of particulate on HVAC components restores energy performance tothe system.The following components in the airstream, when cleaned, are common sources of restored energy performance.
Evaporator Coil: Air is typically cooled in an HVAC system by passing through an evaporator coil. Particulate and other material buildup over time has an insulating effect on the surface of the coil, leading to longer cooling times and greater energy consumption. Additionally, build-up between the fins of the coil increasingly restricts airflow over time. The evaporative coil cleaning process is described in the NADCA ACR (Assessment, Cleaning, and Restoration) Standard.
Heating Coil: Similar to a cooling coil, the heating coil in the furnace plenum is composed of hundreds of narrow air passages. Any restriction in these passages reduces airflow and diminishes effectiveness of the heating. The most frequent cause of a restricted coil is an accumulation of dust, dirt, or other fouling agents. Often a consequence of neglecting maintenance such as regular filter changes, dust and dirt may plug small coil passages and reduce downstream airflow. This degrades the effectiveness of heating throughout the conditioned space. It also increases heating costs as the furnace must run longer to meet thermostat settings. A severely obstructed coil may restrict airflow to the point that the system overheats, tripping a safety high‐temperature switch and automatically shutting down the furnace. The heating coil cleaning process is described in the NADCA ACR Standard.
Reheat Coil: A reheat coil is used in some HVAC systems and looks similar in appearance to an evaporative coil. It is typically positioned near the terminal end of the duct system and acts as a secondary heat source to “reheat” air from the HVAC unit. Reheat coils are used for humidity control and/ or occupant comfort. VAV boxes commonly include reheat coils. Because the spaces between the fins can be quite narrow, they can act almost as a filter, filling with particulate over time. Periodic inspection and cleaning of the coil are needed to ensure proper heating capacity and air distribution in the occupied space.
Turning Vanes: Turning vanes divert air around corners in duct systems to direct airflow. Particle collection can narrow the spaces between vanes, but more importantly, large debris blowing through the duct can get caught on vanes and create significant blockage to airflow. Filters, cardboard, pieces of separated insulation, delaminated insulation, rags and other materials are sometimes found and removed from turning vanes in the cleaning process.
Supply Air Outlet (Register): Located at the end of the supply ductwork, supply registers provide air to the occupied space through a series of blades which are normally adjustable for directional distribution or diffusion. When dirt and debris build up on the register and its blades, airflow can be seriously reduced, negatively impacting energy performance and comfort in the occupied space.
Return Air Inlet (Register): Air flows into return registers from the occupied space to the HVAC unit through ductwork, or in some cases, via an open plenum such as a ceiling plenum. This type of register can get very dirty due to dirt and dust from the occupied space, narrowing the passage way for return air and restricting air movement. Over time it can become completely clogged. Buildup on return registers can result in a system that is severely strained and inefficient.
Fresh Air Intake Screen (Outside Air Screen): Fresh air intake openings in HVAC systems are integral to the quality of the air inside a building. Local codes dictate the amount of fresh air that is required for the health and safety of building occupants. Often a screen or mesh is placed over the fresh air opening to prevent birds, rodents and debris from gaining access into the opening. These screens become plugged by debris in the environment getting caught on the screen or mesh. Screens may also get damp from rain or humidity which causes debris to become “glued” to the screen or mesh. This debris inhibits the proper fresh airflow into the building, which leads to improper pressure relationships within the building and can cause excess build-up of carbon dioxide within the facility.
Fan (Blower): Fans, also known as blowers, move air across the evaporator coil for cooling and the heat exchanger for heating. This is achieved by rotating a series of blades, which are connected to a shaft and driven by a motor. These blades are designed to move a certain volume of air, and particulate build-up on the fan blades, particularly curved ones, reduces the capacity of the blades to move air causing the blower motor to run longer while pushing less air per rotation.
Damper: A damper is a valve or plate that stops or regulates the flow of air inside a duct, chimney, VAV box, air handler, or other air‐handling equipment. Dampers are used to balance and/or control airflows. There are three types: single‐blade, opposed‐blade and parallel‐blade. Single‐blade volume dampers are in branch ducts, typically at the connections to main ducts. Opposed‐ blade dampers are in supply air outlets and are characterised by pairs of damper blades that move in opposite directions. Parallel‐blade dampers are used primarily for mixing air streams. The blades are positioned to operate parallel to one another and direct the airstreams for the maximum mixing effect. The result of excessively dirty dampers is restriction of airflow. Also, heavy particle build-up may restrict the movement of the damper blades, resulting in restricted airflow and possible increased back pressure on the system and compressor. This leads to fans and compressors working harder, increasing energy consumption and reducing equipment longevity.
Sound Attenuator: Sound attenuators use sound‐absorbing fibrous material with perforated sheet metal facings that allow sound energy to pass through and be absorbed by the fibrous fill. This reduces noise emanating from an HVAC system. Also called duct silencers, they sit in the air stream and restrict the airflow through a system of interior baffles. When sound attenuators become dirty or impacted, the amount of air delivered through the duct system is reduced. Depending on the level of restriction, this affects airflow, temperature, and comfort level.
Duct Liner: Internal insulation, also called duct liner, has been used for many years inside ductwork, mixing boxes, linear diffusers, air handlers and many other HVAC components. Fiber glass insulation is most common but other materials may be used as well. The Sheet Metal and Air Conditioning Contractors National Association (SMACNA), which is the industry authority for sheet metal duct construction, has specific installation guidelines for duct liner which, if not followed, can lead to insulation separating from the ductwork. Separated insulation will reduce airflow and loose insulation can blow downstream and land on surfaces such as reheat coils, supply air outlets and volume dampers just to name a few.
Older duct liner may be well bonded to the duct wall but begin to delaminate, shedding pieces of insulation downstream. A careful inspection of any HVAC system will determine if and where any failed or failing internal insulation may be found. Removal of internal insulation will impact the size of the internal cross section of the duct or system component if replacement insulation is not specified. Failure to replace the removed insulation will alter the acoustic properties of the system and will impact thermal performance as well.
Air Straightener: Also known as a flow straightener or air blender, this device is used to straighten the airflow and reduce turbulence in HVAC systems. It is typically found in conjunction with duct sensors. The cross‐section shapes of these “honeycombs” may be of square, circular or hexagonal cells. These straighteners can become clogged with dust and other debris and serve as an impaction point for failing duct insulation and other large debris that have come loose. This will restrict airflow and affect energy efficiency.
Airflow Measuring Station (AFMS): An AFMS is used in an HVAC system as a direct measurement device of the air volume which is circulating through the system. An AFMS could be part of an outdoor air intake louver assembly which measures the volume of outside air introduced into an HVAC system. As airflow varies on a variable air volume (VAV) system, the AFMS controls the position of an outdoor air damper which modulates to maintain the proper volume of outdoor air into the air handling unit (AHU).
There are two main types of AFMS: Differential pressure types that use either a pitot tube array (pronounced pe‐to – described later in this document) or flow ring assembly which measures the velocity pressure of the air and, secondly, a thermal dispersion type sensor which employs a small heater that is used in a mathematical calculation of airflow.
Proper maintenance is required on both types, however the differential pressure type AFMS isprone to calibration issues if the pitot tubes and air lines become clogged. Airflow calculations will be in error if the lines and pitot tubes become clogged with dirt, causing improper control of ventilation (outdoor) air. Excessive ventilation air imposes an unnecessary energy penalty toan HVAC system.
Velocity Sensors/Controllers: Velocity sensors/controllers are used in variable air volume (VAV) terminal boxes to measure airflow that is supplied to a conditioned space. Airflow is controlled over a range of maximum and minimum settings. Additionally, zone heating is often controlled based upon the measured air volume. Velocity controllers operate similarly to the differential pressure type AFMS described in the previous section.
If velocity sensors become clogged with dirt, inaccurate readings will occur, which can cause problems ranging from comfort complaints to increased energy consumption. When the zone temperature is not satisfied, the VAV box damper will open wider, increasing the air handler fan speed and associated brake horsepower (the actual power applied to a motor).
Mist Eliminators: Mist eliminators are designed to eliminate water droplets from the HVAC airstream by collecting them on a surface. These water droplets are then diverted to the drain line system. As particulate builds inside, the eliminator loses its ability to properly remove moisture and reduces airflow through the system. This causes an increase in back pressure and forces the system to use more energy to compensate.
Humidifiers: A humidifier adds water vapor to the air to increase humidity. When installed in an HVAC system, the humidifier or a section of it will be in the air stream and will cause some resistance to air passing by it. Over time, particulate will collect on the humidifier, creating greater resistance to the airflow.
For more details, visit: www.nadca.com
Cookie Consent
We use cookies to personalize your experience. By continuing to visit this website you agree to our Terms & Conditions, Privacy Policy and Cookie Policy.
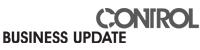