Jack Link’s Snacks, a company from Wisconsin known for producing beef and turkey jerky snacks, sought to expand their production facility twofold. They recognised the necessity of enhancing their refrigeration system.
The expansion included the installation of 50 additional evaporators, 2 air handlers, new condensers, compressors, a recirculator, and a receiver. Consequently, the requirement for an upgraded programmable logic controller (PLC) system to effectively oversee and regulate temperatures and the performance of the refrigerant cycle across the expanded production and storage areas arose.
Solution
Carlson & Stewart Refrigeration, the refrigeration contractor for Jack Link’s, suggested implementing the Danfoss PLC system due to its flexibility and robust capabilities, ensuring it could effectively handle the facility’s requirements while providing enhanced connectivity and efficiency. Jim Orren, Industrial Service Manager at Carlson & Stewart, stated, “We have been working with Danfoss for years, and the products have always met our needs. Jack Link’s was using other electronic components from Danfoss in the plant, and they were working well.”
Easy integration
The Danfoss PLC system is an integrated hardware and software platform that offers programmable set points for refrigeration systems, enabling users to optimise performance. Its graphical interface virtually provides operators with comprehensive monitoring parameters and system operations, ensuring effective control. Additionally, the system enhances safety measures by incorporating ammonia leak detection for early identification of refrigerant leaks.
Utilising non-proprietary hardware and open communication protocols, the Danfoss PLC control system facilitates easy replacement of existing controls, the addition of expansion controls, and integration with refrigeration systems. Newly installed control panels undergo factory testing before being shipped to the job site, and they are configured to communicate with a central control panel remotely. This distributed installation approach significantly reduces installation costs and future maintenance, simplifies commissioning tasks, and shortens project lead times.
Methodology
The new PLC system, with four control panels and a power supply, was installed in 2022. This process entailed retrofitting controls within the existing space and integrating new controls and electrical components, including more oversized fuses. Orren mentioned that after this installation was finished, the start-up of the PLC system proceeded seamlessly.
Danfoss AAIM Controls provides a complete portfolio of components and services for virtually any industrial refrigeration system – providing all-in-one solutions tailored to specific application needs. Brian Davis, head of Danfoss’ AAIM Controls division, said, “We used our expertise in refrigeration and refrigeration system controls to quarantine predicted disruptions and worked cooperatively with the installing contractor and the end user to minimise the “down-time” associated with the upgrade.”
Specification
· System Compatibility: NH3, CO2, Hydrocarbons, and Freon.
· Products: Power, Programmable Logic Controller (PLC) products, and Embedded Microprocessor Control (EMC) products.
· Services: Customised industrial refrigeration products and software paired with onsite commissioning services, remote plant assistance, and digital support tools.
Result
The Danfoss PLC system empowers Link Snacks to monitor temperatures and assess the refrigeration system’s performance throughout their facility. This capability oversees all equipment, such as evaporators, condensers, compressors, air handlers, and ventilation fans, while promptly detecting ammonia leaks. These functionalities have proven invaluable to plant managers.
Eric Siemonsma, project manager at Jack Link, said, “We have better control, visibility and tracking across the plant and can track the system from anywhere in the world. We can see all components and address issues remotely without running to the engine room. The new system saves us time and maintenance costs since the new components are more reliable and have improved.”
Cookie Consent
We use cookies to personalize your experience. By continuing to visit this website you agree to our Terms & Conditions, Privacy Policy and Cookie Policy.
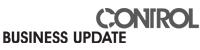