Efficiency of any process plants are defined by the efficiency of the HVAC&R systems installed in the Cooling towers. Industry leaders discuss varied aspects that are booming the industrial demands for cooling towers across the industries.
Cooling towers are a basic requirement in any industry to get rid of the surplus water. They are basically a heat rejection device that pulls the waste heat out of a cooling system. Application of a cooling tower is defined with the industrial requirements. It uses the water evaporation to remove the process heat and cool the working fluid. In case of closed-circuit, dry cooling towers rely solely on air to cool the working fluid to near the dry-bulb air temperature.
The cooling tower market is spread across a wide range of end-use industries, including nuclear and thermal power plants, petroleum refineries, petrochemical plants, food processing plants, and HVAC-R. Therefore, the market is set to nurture as per the growth in other related industries in the coming years.
Talking about the market for cooling towers in India, one should note that cooling towers are relatively inexpensive and highly reliable means for removing low-grade heat from the system. Considering the same, Preyesh Chandrashekar, Business Development Director, National Cooling Towers (NCT), Cooling towers are relatively inexpensive and are considered as a reliable means of removing low-grade heat. “India’s power generation has been increasing at an impressive rate over the last few decades. This further pushes the demand for having HVAC systems and cooling towers across industries; this trend is likely to continue in the coming years. India’s climate policy and low-carbon policy ambition are also drivers for power supply planning in the country.”
This allow the companies to develop a reference scenario to account the effects of the proposed targets and water regulations on the future water demand. Currently, water standards have been specified only for coal thermal power plants (TPPs). Without any additional water standards or regulations, water consumption will increase to nearly seven times of 2010 levels, which is around 14 BCM by 2050.
According to K.P Manoharan, Managing Director, Gem Equipments Pvt., Ltd. Gem Orion Machinery Pvt., Ltd., “Design remains to be the key in allocating the functions based on the applications of a cooling tower. Process can be designed to operate high cold-water temperature and work with air cooled heat exchangers, instead of evaporative wet cooling towers.”
Suresh Sarma, Proprietor, SS Cooling Tower Consultants, talks about the increasing industrial demands for cooling tower. The demands are witnessed across the industries like Solar, Wind energy, cooling, HVAC, large industries, F&B among others. Interestingly, this has imposed more emphasis on lower cost of production. He says “Cooling towers and chiller plants enhances your plant’s efficiency and reduces the carbon footprints from the environment. Your cooling system’s efficiency defines your plants efficiency directly.” A two-degree higher cold water can have an effect of Rs. 5 crores or more on a 500 MW plant. Higher efficient cooling system also improves its availability by lowering the downtime, maintenance and operation cost.
Technological advancements to maintain water flow in process plants
Hanzala Paloba, Filfab Corporation (SMD), here, like to talk about Hydro-flow technology. Hydro-flow technology works by directly inducing an electric field within the water itself, regardless of pipe material or flow rate, which travels throughout the pipe network and protects the entire system of a cooling tower. “This electric field is tailored to a range of applications including lime-scale prevention in anything from coffee machines to power stations, improving the clarity and smell of swimming pools, eliminating bacteria and increasing the efficiency of industrial filtration.”
Hydroflow technology applies an electric signal of +-150 KHz to water inside the pipe without considering MOC of pipe. Since signal goes directly into water, its strength is very high enough to remove already settled scale. The electronic signal flows throughout the water system and cleans whole system. Also, the signal flows to both the sides of machine irrespective of position of machine.
Whereas Manoharan highlights that it’s highly important to reject the process heat coming from power plant, induction furnace or any other process either with direct evaporative cooling or indirect air cooling. Indirect air cooling can be done through air cooled heat exchangers (fin fan coolers) or with chillers in case of low heat rejection process. Both air cooled heat exchangers and chillers consume huge power as compared to the power used by the evaporative cooing tower to reject the same amount of heat. Hence, we either save the water or power, not both in a heat rejection process.
“This is an on-going trend in refrigeration centralised chillers industry, who are now going with water cooled condenser and air cooled dry coolers to save water; designing the compressors with high temperature Freon gases”, he added.
Based on the experience and reviews, air cooled heat exchangers will be an ideal solution to save water. We can have closed loop system and save our equipments and piping from water related issues. Though, we have the technologies to produce power through renewable energy sources, we don’t have a solution for depleting water resources. This is the right time to think about water conservation instead of power conservation in industries and we have a social responsibility about it.
Sustaining the challenges in CT
The major challenge that companies need to overcome is the necessity for water — a scarce resource in India. However, water consumption and dependence of the power sector on water resources are causes for growing concern. Noting the same, Chandrashekhar feels “Several water-intensive cooling technologies are still in use and fossil fuel-based power has a higher direct water footprint than renewable power. Studies in the past suggested that the power sector accounts for a majority of industrial water consumption.
“R&D at National Cooling Towers is an endless process of improvement. Every day we push our boundaries of engineering and manufacturing technology, doing trials and errors for overcoming this challenge and applying it to our wide range of products.”
K.P Manoharan, Managing Director, Gem Equipments Pvt., Ltd. Gem Orion Machinery Pvt., Ltd. Coal power plants will account for the largest share of water withdrawals and consumption, despite having switched over to recirculating (water-efficient) cooling tower technologies.
“Meeting the energy efficiency standards is a task for any industry. It’s imperative to have supportive systems and products, technologies and frequent upgradation to maintain efficiency of your cooling towers” says Paloba.
However, Hydroflow method allows an extremely efficient transfer of energy from the unit, to the pipe and the water contained within. This means that there can be a large, strong signal in the pipe whist the conditioner consumes very little power – around the same as an energy-efficient light bulb. This also means the signal can travel for large distances and throughout the branches of a plumbing system.
The use of an electric field, rather than a magnetic field, coupled with the distance the signal can travel, means the treatment is not dependent on flow rate or volume of water. It also works effectively on both conductive and non-conductive pipe materials.
Sarma, on this note, suggests few key developments that need to be implemented for promoting water management at thermal plants:
• More use of sea water as the cooling media
• Higher operating COC
• Reduce drift by using upgraded technology
• Use a combination of dry and wet cooling
• Use of hybrid cooling technologies
• Cooling tower has three major zones of mass transfer: the nozzle, fill and the rain zone. The fill zone usually contributes about 75 per cent cooling in the tower.
Key factors to contain efficiency
A dry cooling tower operates like an automobile radiator. There is no direct contact with air and thus there is no loss of water from DCTs. Hence, there is an increasing interest in dry cooling towers, also known as Closed Loop Cooling Towers, in areas where water scarcity prevents plants from using a traditional water-cooled condenser in a steam power plant but with only low-temperature difference depending on the ambient weather conditions. “We have manufactured and commissioned such Closed Loop Cooling Towers also known as Air Blast Coolers”, says Chandrashekhar.
With industrial growth in Indian region, the demand for heating and cooling of utility has increased exponentially. Chalking down the essential aspects to enhance efficiency, Paloba mentions of Filfab’s application; Prevention and Removal of existing Limescale.
The limescale is formed due to change in temperature and pressure, which saturates the molecules of calcium and bicarbonate ions in the water, hence forming limescale in the system.
Hydroflow Technology models can work with any systems for removing their existing limescale as well as it will not allow new scale to settle on to piping surface. Since scale is always present in the water, based on changes in temperature and pressure scale settles on internal sides on pipes, tubes, etc. Hydroflow Electronic water conditioner ensures removal of existing scale and will not allow new scale to settle. This will work with Shell and Tube Heat exchanger, Plate Heat exchanger, Cooling Tower, Any Boiler, Evaporator, etc.
Major factors affecting cooling tower performance
• Fill performance may be lesser than anticipated
• Fan power provided may be lesser than required
• Distribution system may not be optimum
• Fills may be clogged, damaged or missing
• Fan may be working at lower efficiencies or at higher pressure and hence lower air flows
• Obstruction at tower inlet
• Low air inlet heights causing high inlet velocities thereby causing areas of poor air flow
Paloba, here highlights the benefits of installing cooling towers. One of the most immediate and obvious benefits of this approach is the ease of installation. The conditioner can be fitted on to a pipe or plumbing system without the need to cut or make modifications to the existing pipe work.
This allows for quick, easy installation, with no downtime. This technology can be applied to extremely large pipes – in fact, it has been used on pipes with diameters of over one and a halfmeter, and can be used for still larger pipes where the signal can travel great distances – up to hundreds of meters. It can be used for a wide range of applications, from hot water production in large residential and commercial buildings to more industrial applications including steam production in high pressure steam boilers, copper mines, steel mills and power stations. Some benefits are;
• Lime scale removal
• No new lime scale formation
• Bacteria, algae growth reduction
• Significant reduction in chemical usage
• No regular need for downtime for maintenance
• No AMC, no moving part
• Long life
In any heat exchanger system, the scale deposits in the tube of heat exchanger for e.g. condenser, chiller, boiler, evaporator, etc. The Hydroflow Technology effectively removes existing limescale and doesn’t allow the formation of new scale. The continuous process of conditioning the water ensures that system is kept free from deposition of scale and hence enhances life of a system.
Final note
Thermal performance upgrade has become one of the important aspects in overall plant efficiency. An important factor is to provide improved cold water outlet in the cooling tower. A thermal performance upgrade is necessary to improve cold water (provide guaranteed improvement in cold water at tower outlet), reduce drift loss, improve fill and condition of other deteriorated components, possible reductions in power consumption, and reduce maintenance cost and equipment down time.
Your cooling system’s efficiency defines your plants efficiency directly.”
Suresh Sarma, Proprietor, SS Cooling Tower Consultants
India’s climate policy, energy generation and consumption pattern, and its low-carbon ambition are having more of efficient HVAC systems in the country.”
Preyesh Chandrashekar, Business Development Director, National Cooling Towers (NCT)
It’s imperative to have supportive systems and products, technologies and frequent upgradation to maintain efficiency in cooling towers.
Hanzala Paloba, Filfab Corporation (SMD)
CT’s process can be designed to operate high cold water temperature and work with air cooled heat exchangers, instead of evaporative wet cooling towers.
K.P Manoharan, Managing Director, Gem Equipments Pvt., Ltd. Gem Ori
Cookie Consent
We use cookies to personalize your experience. By continuing to visit this website you agree to our Terms & Conditions, Privacy Policy and Cookie Policy.
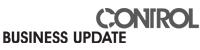