Integrating MEP systems is critical in optimising HVAC solutions for residential, commercial, and multi-use buildings. MEP integration with HVAC systems is essential for future predictions and efficient operation. MEP project management software enhances productivity, tracking and reporting, facilitating better decision-making throughout the project lifecycle.
The initial building layout sets the stage for a project’s success in architectural design and construction. Vital to this success is integrating Mechanical, Electrical, and Plumbing (MEP) systems seamlessly into the building’s framework. As the project evolves, changes in interior structures and equipment additions often become necessary, impacting essential MEP services such as plumbing, firefighting, HVAC, and electrical systems. These systems are intricately tied to the building’s structure, with services running through slabs and floors.
Alterations in interior layouts, common in projects spanning extended durations, often necessitate adjustments like rerouting ducts or modifying water flow in HVAC systems. Two key factors emerge during initial building design: building orientation and space planning for services. An improper orientation can increase cooling requirements through glass surfaces, raising capital and operational costs. Mr. Khan Moid Hasan, Director, Black & White Engineering, noted, “Adequate space allocation for elements like Air Handling Unit (AHU) shafts is crucial to facilitate service transfer between floors and avoid cramped equipment spaces that hinder maintenance efforts. Comprehensive planning from the project’s inception ensures that everything from building orientation to the placement of MEP components is meticulously addressed, promoting project success. However, unplanned building orientation or layout adjustments can introduce complications, challenging architects to adapt without compromising essential services.”
According to Mr. Dipak Babrekar, Principal Consultant and founder of Benchmark MEP Engineering Consultancy & Training, adopting Building Information Modeling (BIM) in conjunction with MEP Virtual Design and Construction (VDC) is gaining momentum among architects and designers. This dynamic duo streamlines the coordination process, enhancing overall project efficiency and adaptability. While these advanced tools can reduce challenges, their effectiveness depends on meticulous planning from the project’s outset to avoid potential pitfalls and ensure project success.
Streamlining Maintenance Efficiency through Collaborative Planning
In construction and facility management, minimising downtime is a top priority. The key to achieving this goal lies in the initial planning stages of a project, where careful consideration is given to equipment access and selection. It’s a common scenario – equipment is efficiently installed during the construction phase, but when it comes to maintenance, the lack of clear access or provisions for servicing becomes evident. This oversight can result in prolonged downtime, disrupting operations and causing frustration. To address this challenge head-on, engineers and architects must collaborate closely, ensuring that maintenance requirements are integrated from the project’s outset. This collaborative approach is a game-changer, helping to minimise downtime and enhance overall operational and maintenance efficiency. Ultimately, the secret to reducing downtime lies in diligent equipment maintenance, emphasising the importance of proper planning and accessibility from the project’s inception.
Innovative trends in HVAC for a sustainable future
Manufacturers are gearing up for the future with a strong focus on energy efficiency. Mr. Aman Sachdeva, Secretary, ISHRAE Gurugram Chapter, says, “The market is witnessing the emergence of energy-saving technologies, emphasising energy conservation and water resources. Utilising return water is a standout feature in the upcoming generation of HVAC (heating, ventilation, and air conditioning) equipment. This groundbreaking approach aims to recycle water before it returns to the chiller, addressing the growing concern of water scarcity. An innovative strategy involves minimising condensation on HVAC system coils, which helps maintain a minimal temperature difference between return and supply water. This reclaimed water can then be redirected to spaces requiring higher temperatures, effectively recycling it to ensure optimal conditions throughout the building. This forward-thinking approach conserves water and significantly enhances the efficiency of HVAC equipment. The future of HVAC is undoubtedly green, offering sustainable solutions to meet the world’s evolving energy and water challenges.”
MEP systems for production facilities
In many Indian factories, the focus has traditionally been on ventilation rather than air conditioning, with cooling systems primarily dedicated to the production process. Comfort and air quality have often been secondary concerns. Citing an example, Mr Hassan shared that there are exceptions, like a factory in Gujarat operated by a German company that manufactures railway maintenance equipment. This facility is fully air-conditioned and equipped with systems to ensure excellent indoor air quality, even in areas with processes generating smoke, such as grinding and welding. This example highlights the potential for broader adoption of air conditioning in factories to create a healthier and more comfortable environment for workers.
Mr. Shankar Ghime, Chief Consultant and Energy Auditor at Air Technics MEP Consultants, adds that the industrial landscape varies greatly, ranging from facilities with no air conditioning to fully air-conditioned factories. For instance, pharmaceutical factories heavily rely on air conditioning, while certain industries have minimal air conditioning.
In the process industry, air conditioning and refrigeration play vital roles. Temperature requirements can fluctuate, ranging from as low as 10 degrees Celsius to 22 degrees Celsius. In cases where temperatures exceed 20 degrees Celsius, it’s possible to reduce reliance on chillers and opt for water-based cooling systems. This approach is feasible in dry regions like Delhi or Nagpur but may only universally apply in some parts of India.
In the food industry, most projects focus on comfort air conditioning or process air conditioning, with a significant emphasis on moisture removal to maintain product quality. There’s room for equipment modifications to address moisture-related challenges and ensure product quality.
MEP integration for commercial buildings
Mr Sachdeva explains that tailor-made HVAC solutions are essential to tackle specific challenges in diverse manufacturing settings, such as tar and automobile industries. For example, effective ventilation is a critical consideration in industries dealing with high temperatures like tar production. Our approach has involved implementing two-stage and three-stage evaporation systems, particularly in arid regions.
When it comes to enhancing HVAC energy efficiency in commercial buildings, a multifaceted strategy is required. This strategy includes MEP integration (mechanical, electrical, plumbing) and the implementation of building automation. The effective design of electrical systems, precise pipe sizing, and the central role of automation are key components. Automation, in particular, significantly contributes to energy savings by optimising building management systems chiller plant operations, and employing efficient algorithms. Numerous energy measurement and monitoring systems offer valuable insights for improvements in HVAC efficiency.
Software tools
In software, the current focus is on utilising platforms like Revit and BIM 360. These tools enable seamless collaboration among stakeholders, including MEP, architecture, and structural teams, allowing for effective coordination. Mr Hassan says, “While these platforms offer plugins and features to enhance performance, the ultimate efficiency depends on how well we leverage them for service integration and coordination.”
Efficiency in HVAC planning is greatly influenced by meticulous design and space allocation. Practical experience has shown that insufficient space for ducts or equipment placement can lead to challenges. Additionally, inadequate space for equipment maintenance, like filters in AHUs, can increase energy usage when pressure drops occur. Properly planning and coordinating spaces is essential, as fresh air intake, for instance, significantly impacts the load on air conditioning systems. With adequate planning and coordination, it becomes easier to implement energy-efficient solutions like heat recovery systems requiring sufficient space.
Building Management Systems
Integrating IoT (Internet of Things) technology and sensors is revolutionising Building Management Systems (BMS), offering real-time data on parameters like temperature, air pressure, and energy consumption, providing a comprehensive view of building performance. Virtual reality also transforms the industry, enabling remote meetings and site inspections.
Indian-made software is democratising advanced HVAC management, even for those without specialised expertise, essential in achieving net-zero energy goals and complying with rigorous standards, especially in pharmaceuticals.
Historically, the high costs of BMS and IoT sensors limited their use in industrial settings. However, MEP (mechanical, electrical, plumbing) consultants increasingly advocate for their incorporation. Advanced sensors monitor critical elements like filter conditions, enabling maintenance schedules based on specific parameters, conserving energy and streamlining maintenance operations.
Cost remains a central concern when suggesting IoT and AI technologies to clients, with integration potentially increasing MEP costs by 25% to 30%. However, Indian manufacturers producing IoT sensors are expected to reduce costs, making these technologies more accessible.
ROI and Building Efficiency
Regarding building management, return on investment (ROI) is a make-or-break factor. Consider solar panels, initially offering a 5-year ROI. Neglecting proper maintenance can extend that period to 7 years or more. The lesson here is clear: ROI is inextricably tied to operational efforts. To reap the rewards, you must allocate resources for capital expenditure (capex) and ongoing operational expenditure (opex). Investing without ongoing maintenance won’t yield quick returns, a principle that extends beyond solar panels to various equipment where ROI hinges on operational costs.
A compelling case study of a hotel’s energy consumption illustrates the value of automation, mainly Building Management Systems (BMS). The hotel integrated BMS around five to seven years ago, leveraging data to pinpoint areas for automation-driven efficiency. Astonishingly, the initial capex for automation was recouped solely through energy savings within a few years. After five years of automation implementation, substantial energy savings covered nearly 70% of the capex. This case underscores that substantial ROI is attainable within a relatively short timeframe, typically six to eight years, with effective maintenance and operations. The applicability extends to integrated 500-ton HVAC systems and associated enhancements.
Furthermore, the strategic coordination of Mechanical, Electrical, and Plumbing (MEP) services during the design phase, while incurring an initial cost for advanced tools and consultancy services, reaps numerous rewards. Effective coordination during design significantly diminishes issues during construction, saving time and benefiting the client. The time saved translates into the early opening of properties like hotels, contributing to operational savings and cost-saving benefits for clients. Beyond the buzz of ROI, effective coordination in building management ushers in tangible gains.
Shankar Ghime, Chief Consultant & Energy Auditor, Air Technics MEP Consultants
“Effective coordination of MEP services during the design phase significantly reduces issues during construction, saving time and benefiting the client. This time-saving can lead to earlier project completion.”
Aman Sachdeva, Secretary, ISHRAE Gurugram Chapter
“A multifaceted strategy is required to enhance HVAC energy efficiency in commercial buildings. Automation, precise pipe sizing, and the central role of automation are key components.”
“The adoption of Building Information Modeling (BIM) in tandem with MEP Virtual Design and Construction (VDC) streamlines the coordination process from design to operation, improving overall project efficiency.”
Dipak Babrekar, Principal Consultant & Founder, Benchmark MEP Engineering Consultancy & Training
“IoT sensors can significantly reduce maintenance costs and improve energy efficiency. Sensors can monitor elements like filter conditions and eliminate the need for regular preventive maintenance.”
Cookie Consent
We use cookies to personalize your experience. By continuing to visit this website you agree to our Terms & Conditions, Privacy Policy and Cookie Policy.
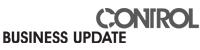