HVAC systems are typically designed for a relatively long life or around 10 – 15 years for common applications, and if maintained properly, will be able to deliver cost effective operations.
Modern chillers are redefining how energy is used in this traditionally energy intensive product, especially when seen in the commercial building space, where the HVAC system can account for over 45 – 50 percent of the energy costs for the owners. Just a decade back, an Indicated kW (ikW – the amount of energy needed to remove a specific amount of heat form the system) of under 1 would have put a smile to the system operators. With advances in technology such as variable frequency drives, variable pitch compressors etc., the ikW came down to 0.7 – 0.8 and we are now seeing a proliferation of Magnetic chillers that have been able to achieve an ikW of below 0.5. Thus, the last decade has seen the energy efficiency of chillers drop by 50 percent, which is no mean feat for any industry. How much more efficient do the chillers of this decade become, is something that we are all waiting to see.
While new installations have high efficiency chillers where the building owners are willing to invest in them, there are several chillers in use across the commercial building landscape in the country that is not as efficient. Coupled with older system components that also have a degree of inefficiency, the overall efficiency of the HVAC system is higher than the new developments. This is a direct cost for the building occupants and hence, can be a reason for a tenant to move to a more efficient building if other factors remain to be the same. In the current situation where organisations are relooking at all operating costs minutely, operating older chillers with higher energy usage is a business disadvantage. An effective maintenance plan that helps the chiller and associated systems to work optimally and at the design points will help building operators in keeping the HVAC costs of the older chillers low and in turn reduce operating expenses for the occupants. This article discusses the reasons for inefficiencies in the HVAC system and how Maintenance can eliminate these inefficiencies and restore the system to the design operating point or even exceed originalenergy usage values.
Why HVAC systems become inefficient during the life of the building
A building HVAC system is a complex system, with many variables such as internal/external operating conditions, workspace load, workspace design and use, etc. In addition, this is a multi-component system – chillers, primary and secondary pumps, cooling towers, AHUs, piping, etc. The overall system efficiency thus depends upon many components and factors as shown in figure 1. In a new building, all the components are new and operating at their design efficiencies. However, as the building ages, components age as well and, in many cases, sub systems get retrofitted (one chiller gets replaced by a newer chiller due to a major breakdown) or modified (meeting room changed to work stations!) which effects the overall system. In addition to these factors, another key reason for an inefficient HVAC system is poor or improper maintenance.
A HVAC system has many moving components, many operating at high speeds and in harsh conditions (dust, humidity etc.) and hence, the entire system needs a high level of upkeep and maintenance to enable the system to run at design efficiency. The systems are typically designed for a relatively long life (10 – 15 years for common applications) and if maintained properly, will be able to deliver cost effective operations.
An Effective HVAC maintenance approach
Maintenance Philosophies: There are three commonly used approaches to maintenance as shown in figure 2. Many building owners, to save on costs, follow the “run to failure” philosophy which is also supported by the built-in redundancy in systems that most buildings have. This, however, is not a good solution in the long run as there is high degree of uncertainty of the system and overall life cycle costs are high. Preventive maintenance is the approach that most progressive and mature building owners adopt as it allows the equipment and systems to be maintained in a particular manner with regular frequency, allowing for a higher uptime and reliability. The downside of this approach is that maintenance may be carried out even if the system is working fine and does not need the activity. Most OEM’s recommend this approach as it is easy to implement and is low risk. The most effective approach to maintenance is of predictive maintenance where the condition of the equipment’s/systems are analyzed using various techniques such as oil analysis, vibration monitoring, electrical load assessment etc. Maintenance is then undertaken based on the condition of the system – some critical maintenance activities are still done in a fixed frequency, but the majority are governed by the condition. This approach enables maintenance when it is needed and lowers overall cost of ownership.
HVAC System Maintenance Best Practices
Which maintenance approach to adopt –Predictive or preventive or a combination of both depends on the HVAC system use as well as cost appetite of the system owner. Both approaches work and if implemented effectively, will enable the O&M team to run the HVAC system at peak efficiency. The run to failure approach may also be used in the end of life scenario where the number of failures is typically higher as the number of failures follows the “bathtub” curve (Figure 3). Some of the best practices that the maintenance team can adopt to enable the HVAC system to operate at the highest efficiency levels are:
Whole system approach: The chiller is the most expensive and critical part of the HVAC system and it is nut natural that a lot of maintenance effects are focused on this component. However, the chiller does not work in isolation and the entire system must be working at peak efficiency for the chiller ikW to be close to its design value. Thus, the maintenance plan should cover all components such cooling towers, pumps, AHUs, water systems etc.
Water Quality: Maintaining the hygiene of the primary and secondary water systems is of the utmost importance but not enough attention is given to this aspect by building maintenance teams. OEM’s recommend the key properties of water that need to be met (TDS, pH, hardness, microbiological content etc.) and maintenance teams need to ensure that only water meeting these values is used in the system. Regular checking of parameters at multiple points is essential to know the quality of the water and act quickly in case there is a deterioration in the parameters.
System Hygiene: Simple actions like keeping the AHU filters clean will go a long way in keeping the HVAC system working at peak efficiency. Poor condition of Heat exchangers is a major source of system inefficiency – In water cooled chillers, high approach temperatures are indication of fouling of the tubes and can increase energy use by 8 – 10 percent. Therefore, a well-planned out maintenance plan for the heat exchangers including periodic cleaning of heat transfer surfaces will enable the system to operate at the desired efficiency levels.
Data Logging and Trend Analysis: The task of the maintenance team does not end once the maintenance tasks have been completed. A critical aspect of an effective maintenance program is to record operating data effectively and then undertake regular trend analysis of the key parameters to identity any systems or equipment’s that may be starting to deteriorate. Modern buildings have advanced BMS systems that carry out such analysis but older buildings or ones where the BMS system is not fully integrated or does not have trending functionality will need to rely on old school data analysis based on physical logbook data.
Conclusion
A large stock of commercial buildings has chillers and HVAC system components that were designed 10 – 15 years back and have been in operation for more than 5 years. Chiller and associated systems have become more advanced and efficient in the last 5 – 10 years but the legacy systems can’t be changed due to the residual life left and the costs involved. These legacy systems if not maintained effectively operate less efficiently and in turn consume more energy. An effective maintenance strategy and adequate focus on maintenance by building owners, along with the messier funding is essential to operate the overall HVAC system at peak efficiency. This will lead to lower breakdowns, lower operating costs, lower lifecycle costs and ultimately, increase the life of the asset for the owners.
This article was authored by: Aneesh Kadyan, Executive Director, Property Management, CBRE South Asia Pvt. Ltd.
Cookie Consent
We use cookies to personalize your experience. By continuing to visit this website you agree to our Terms & Conditions, Privacy Policy and Cookie Policy.
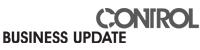