Pre-fabricated cold storages panels can ensure high thermal efficiency and low heat transmission, further minimising the overall load in a refrigeration unit.
Adoption of new modern technology concept where a complete study of existing construction system is done from basic civil infrastructure to insulation system can take care of existing problems. The massive civil construction involving RCC and brick works also needs to be given a thought. Suppose the brick wall and insulation system is replaced by a system which will serve the purpose of a permanent wall and insulation as a composite system then it becomes very convenient.
This is exactly where modern technology comes. Now we have prefabricated panels that can be permanent walls and insulation, which can further be used for roofs. These panels have closed cell insulation (PUF) and faced on both sides with colour coated steel. These metal sheet bi-facial panels act as vapour barrier and resist flow of moisture from both sides. These steel panels provide mechanical strength and sturdiness in harsh environmental conditions, and do not have any thermal bridge in between to allow heat conduction.
Panel construction
The panel system consists of basic pre-fabricated panels made to very tight specification and the full range of accessories required, including insulated doors, pressure relief valves, sealants, mastics, PVC and aluminum profiles, ceiling suspensions and plastic components.
The inner and outer surface of each pre-fabricated panel is made of a 0.5 / 0.6mm thick hot dipped galvanized steel sheet and sandwiched between them is a 40+2 kg/m3 layer of rigid CFC free close cell and also HCFC free and zero ODP Polyurethane foam. Each panel is furnished with a tongue and groove joint and is optionally provided with cam locks jointing arrangements to ensure rigid interlocking between panels.
Each panel is painted with a colour coating of 20-25 microns of architectural polyester on a minimum 175 gms/m2 base of zinc coating. PVC and plastisol coatings of 200 micron thickness are also available as an option. The standard colour is off-white and the surface of the steel sheets has light- cutting grooves both to enhance their strength as well as to provide an aesthetic appearance. Plain panels are also available. Panels are usually approx. 1M wide and transportable length up to 12-13 meters.
The pre-fabricated panels are built with a wide variety of doors, hatches and see-through glasses. Moreover, these doors can be hinged or sliding, manually operated or mechanised.
Usually, standard mechanised doors are designed with a dimension of 1300mm x 2300mm and have electrical heat tracers to prevent freezing of gaskets. Manual sliding doors are designed at a size of 2200mm x 3000mm and normal hinged door of 1220mm x 2010mm.
These panels are manufactured in a semi automated or fully automated continuous machines, with total quality control. The panels are indigenously manufactured and easily available in the country (approx. mfg. capacity 20 million sqm. per annum).
Installation of panels
These panels can be directly bolted to the RCC columns with apposite binding arrangements. It can be of two kinds:
In one method, after fixing the panels horizontally the joints on the column is covered by a flashing.
In other type the panels are fixed with a hidden fastening arrangement, which makes an absolute flushed finish. In both case, panels are fixed horizontally and the columns are inside visible only. Outside an absolute smooth wall will be noticed.
The RCC columns can further be replaced by steel columns, rafters and purlins. This technology of steel is also termed as Pre- engineered Building concept. The entire RCC framework is replaced by structural steel components (vertical-columns, horizontal – rafters). The columns are usually placed at 4-5 meters. These steel structures are lighter than conventional steel structure. The steel columns and rafters are tapered reducing the steel consumption. Wall panels are fixed vertically to these purlins. Wall panels can have a maximum length of 12-13m length. Here, horizontal purlins will be on top and bottom, fixed to the columns. The entire steel fabrication is done at the factory and brought to site in knock-down condition, thereby reducing any welding function at site. This makes construction faster without having site welding.
The roofing arrangement here is a 2-tier system. A false ceiling, with pre-fabricated PUF panels is hung from the roof structure. An insulated „T‟ arrangement is through, on to which panels are placed. Over the steel structure, profile colour coated steel sheet is provided, which stops direct heat or rain to come in contact with the panels below. Exhaust fans are provided to blow out the heat accumulated in between the roof and panels. Chilled water pipes can be carried in this space.
The construction time required for a typical 5000 tons cold storage with steel PEB structure can be approximately of 90 days. Since time period is short, construction can be taken up 2-3 months before the harvesting time and save interest period.
Main features of the Panel system are:
- A high strength to weight ratio, with significant savings in steel work and load bearing foundations, allowing large spans to be constructed with no intermediate columns
- Dimensional stability
- Maintenance-free surface
- High thermal efficiency ensures low heat transmission, resulting in lower refrigeration load
- No deterioration of thermal efficiency overtime
- Panels can be furnished in single jointless height / Length up to 12 meters. Partition wall can be easily erected as the panels are self-supporting
Panel system incorporates special “L” shaped single piece panels for CORNERS. This avoids wall to wall direct jointing – provides additional stability, strength, aesthetical appearance, easy housekeeping etc. - To arrest thermal leakage, joints are finished in tongue and groove configuration which in combination with cam-locks (optional) ensures a foam to foam joint rather than a metal to metal joint.
For additional reinforcement “U/L” shaped flashing are provided at wall to ceiling joints. - Basic advantages of modular construction of cold storage
- It provides the best possible Thermal Insulation value achievable.
- Overall construction period is reduced to a great extent.
- With Modern Cold Storage Construction with PU Panels, the internal atmosphere becomes complete hygienic and resistant to fungal attacks. According to available data, this accounts to 30 percent savings of stored products.
- The deposition of any kind of impurities over the panels or holes being created by fungus / rats is entirely ruled out.Are maintenance free, and trouble-free cleaning and washing.
- Such systems are in use in the country for more than ten years now.
For more details, visit:
www.lloydinsulation.com
Email: kk.mitra@lloydinsulation.com
Cookie Consent
We use cookies to personalize your experience. By continuing to visit this website you agree to our Terms & Conditions, Privacy Policy and Cookie Policy.
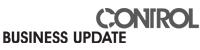