Natural refrigerants are expected to stay forever. But, this we see new challenges in the HVAC/R industry.
The “price to pay” for avoiding refrigerants with high global warming potential is not so low: high pressure, flammability and/ or toxicity. The search for more and more efficient systems presents an additional challenge. In this context, the choice of the right technologies to optimise the use of natural refrigerants becomes essential! The following five questions can help as a starting point when designing a system: Which natural refrigerant is the most suitable for my application? This question is generally easy to answer, considering the different characteristics of each type of natural refrigerant.
Hydrocarbons have been proven to be suitable refrigerants for small units, such as beverage coolers or plug-in units, where the refrigerant charge is low enough as to make flammability issues less relevant. CO2 has started to be widely used in applications ranging from centralised systems in supermarkets to air conditioning systems for vehicles. Ammonia has been mainly used in industrial refrigeration for many years. However, its use is now being extended to other applications, such as commercial refrigeration as a secondary fluid. In any case, developments are allowing the use of refrigerants in applications where they had previously not been used and thus, a detailed study of the requirements of each system is recommended before choosing the refrigerant. Where will the application be located? On one hand, when using CO2, it is important to know the climate conditions of the place where the system will be located. In general, for systems with a condenser/ gas cooler located outdoors, the outside temperature can determine the most suitable type of cycle and technologies.
In practice, if the outside temperature reaches the critical temperature of CO2 (31.2°C), the system will work in transcritical mode (except for cascade or pumped systems) and thus efficiency will be lower. There are different technologies available that can help increase efficiency at high temperatures: parallel compressors, ejectors, FTE…On the other hand, installing the equipment outdoors and/or out of the reach of people when using a flammable or toxic refrigerant (hydrocarbons: flammable; ammonia: toxic and mildly flammable) can make it easier to comply with the relevant standards and make the installation safer. Which regulations and standards need to be respected? This is one of the toughest issues to face. As regards regulations, these are currently focused on reducing the global warming impact of refrigerants, thus the use of natural refrigerants is highly recommended.
Attention therefore needs to be paid to the safety standards. The safety standards to be complied with while using natural refrigerants depend on the application, the type of refrigerant and the country. There are general standards, such EN 378 in Europe, and product standards, such EN 60335-2-89 for refrigerating appliances with up to a certain refrigerant charge. These mainly include special requirements for systems using flammable refrigerants, but there are also some requirements for systems with CO2. What type of cycle should I design? The evolution of natural refrigerants has led to different types of systems for each refrigerant. Starting with the traditional layout for CO2 (essentially comprising a compressor, an expansion valve and two heat exchangers), its low efficiency has led to the development of different alternatives.
On one hand, it is possible to keep CO2 in a subcritical state by designing a cascade or pumped system. CO2 is used in a secondary low temperature loop: either vapour compression (cascade system), pumped loop of liquid CO2 (pumped system) or both (hybrid system). On the other hand, transcritical CO2 systems can have single or dual evaporator, the latter being called a booster system. The first option consists in adding two valves and a receiver to the traditional layout, so that simultaneous control of gas cooler pressure and evaporator superheat can be achieved, together essential for optimising the efficiency of transcritical CO2 systems.
However, this solution can be made even more efficient by adding parallel compressors, so that the refrigerant coming from the receiver is no longer expanded but rather flows directly into the compressors in the parallel line. If an ejector is added to the three-valve layout with parallel compression, system performance is improved even further, in almost all warm climates. In simple terms, an ejector is a device capable of using the potential energy of the high-pressure refrigerant to draw in low pressure refrigerant and bring it to an intermediate pressure, thus reducing the compression ratio and the flow-rate handled by the compressor. Working with a three-valve system featuring a multilevel liquid receiver and zero K superheat evaporators (FTE) is another way of increasing the efficiency in booster systems. Layout of a CO2 transcritical system with ejector.
As concerns propane, the traditional cycle with a compressor, an expansion valve and two heat exchangers usually perform even better than with HFC refrigerants. There is another option, i.e. to make a multi-circuit system, if the refrigerant charge is higher than the maximum charge limit allowed by the corresponding safety standard.
Lastly, there are different types of systems that can be used with ammonia as the refrigerant and that have been successfully implemented on the market. Ammonia vapour absorption refrigeration systems are one of the oldest refrigeration systems, yet are not very popular now due to low efficiency. Single-stage compression systems comprise the same components as a traditional refrigeration system, as well as a pump and a liquid separator, to ensure that the compressor does not receive any liquid. Two-stage compression systems are the next evolution of industrial refrigeration systems, suitable for low temperature refrigeration applications, providing high efficiency and low compressor discharge temperatures.
Additionally, low-charge ammonia systems have emerged in recent years. On one hand, optimised systems comprise a traditional industrial ammonia refrigeration system further optimised by low-charge components. On the other, a packaged ammonia system eliminates the huge quantities of ammonia inventory and piping by moving to smaller self-contained systems that are usually placed on the roof/ground outside, avoiding any dangers due to leaks. Ammonia is also chosen as the refrigerant in both traditional and low- charge cascade systems, normally on the high temperature side, limiting its use to the equipment room. Can energy efficiency be improved? If you have already chosen the cycle to design, you may also have thought about incorporating high-efficiency technologies.
These, combined with an efficient control and supervisory system, can be key to obtaining a system with optimised performance. On one hand, variable-capacity compressors with inverters provide the best way to avoid inefficient on/off cycles that reduce the compressor’s seasonal efficiency. This means that, at part load or in low load conditions, an inverter-driven compressor adapts its cooling capacity to the system requirements without stopping completely. The ideal solution is to combine variable-capacity compressors with Electronic Expansion Valves (EEV), which bring energy savings due to adaptive optimisation of system operating parameters. There are other components that can increase efficiency and are mainly used in CO2 systems. A sub-cooler exploits the gas temperature after expansion in the flash valve to cool the liquid refrigerant before the EEV. An economizer is a type of sub-cooler that extracts a small amount of CO2 from a specific point in the system and expands it through an expansion valve in order to cool the main flow coming from the gas cooler. Lastly, evaporative cooling in CO2 refrigeration systems reduces the temperature of the gas cooler by spraying micro particles of water, bringing significant energy savings due to the reduction in power consumed by the compressor. These solutions are especially suitable to increase the efficiency of CO2 systems in warm climates.
Cookie Consent
We use cookies to personalize your experience. By continuing to visit this website you agree to our Terms & Conditions, Privacy Policy and Cookie Policy.
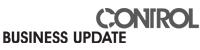