A cold storage is a building or a group of buildings with thermal insulation and a refrigeration system where perishable food items can be stored for a longer period of time under particular temperature conditions, humidity, and appropriate environment to slow down deterioration and spoilage, which would occur in a natural environment. In some countries, cold stores are known as refrigerated warehouses.
Thermal insulation system is a combination of material and ancillaries for application and application methodology, which resists the flow of environment heat to the interior of a building or enclosure that is supposed to maintain a much lower temperature than the exterior (a typical Indian situation where ambient temperatures are higher during most of the year). Thermal insulation will resist the flow of heat by acting as a barrier. The most effective insulation will provide maximum resistance and will be defined by a particular “R” value which will depend upon its thermal conductivity value and thickness. The lower the thermal conductivity of an insulation material, the more effective it will be. Further, mass of the insulation material is also important and is defined as adequate density of the material to be selected.
In a cold store operation, a refrigeration system brings down the temperature initially during start-up, but thermal insulation continuously maintains the temperature later on.
Cold stores nowadays are insulated with prefab panels — usually polyurethane foam sandwich panels comprising CFC-HCFC free closed cell polyurethane foam insulation of density 40–45 kg/m3, having thermal conductivity value of 0.023 W/mK, and faced with colour-coated galvanised steel sheet. The panels are manufactured from continuous line machine and finished with tongue and groove edges and typical width of 1.2 metres, length up to 13 metres and thickness ranging from 30–200 mm, though the international market has up to 300 mm. A higher thickness provides improved energy conservation and extended time period of temperature maintenance during power failure/shutdown.
In addition, PIR is Class “O” rated as per BS:476 Parts 5 and 7. This makes PIR panel fire-safe. Further, PIR panels are tested for “1 Hour” fire rating as per BS EN 1364-1: 2015. This signifies that in the event of a fire inside a cold store, up to 1 hour fire will not affect the panels. This is important for evacuation or for the fire services to get into action. During cold store construction, there can be instances of fire due to welding sparks coming in contact with foam or cables catching fire, but a fire rated panel will not get affected. There have been instances of cable burning, but only the portion where the cable passes the panel bears the burn marks.
The future trend of cold store construction will involve fire rated PIR panels.
Thermal insulation is not material alone; it is the complete system which includes how it is applied and finally finished or the cladding/covering arrangement which provides protection. Proper application technique is equally crucial to its success.
In case of cold stores where a lower temperature is maintained, insulation has a major role to play. Insulation will resist the flow of heat from outside. If insulation does not perform effectively, cold loss from inside will take place and load on refrigeration will increase.
Now let us look into the functioning of cold storage and how insulation failure can be identified and what the causes are. Cold store comes under cold insulation. Cold insulation is also defined as anti-condensation insulation. Whenever there is a situation of a cold body and humidity is present all around, heavy condensation deposition on the cold body will take place, which will make the entire area moist. A more severe situation can be icing formation. Now, even if insulation is done over the cold body, condensation will still take place as water vapour will pass through the insulation joints. So a vapour barrier is used, which is a solid impervious membrane applied over the insulation joint on the warm side that avoids the water vapour or humidity to pass through it. Vapour barrier is very important in cold insulation. Along with vapour barrier, a proper adhesive and fixing of insulation within a holding framework is essential so that it remains in place for a longer period and performs effectively.
Existing conventional cold storage situation: Introduction
Cold storage, primarily meant for potato storage, is an industry existing since independence. These cold storages, usually running from capacities of 2,000–6,000 tonnes, are found in the co-operative and private sectors. The usual height, on an average, is 40–50 feet, and the base is like a square of various dimensions, depending on the capacity. The main construction methodology involves erection of RCC columns on the periphery, thick brick walls, asbestos sheet roofing fixed over a steel structure or RCC roofing, and a false ceiling.
The inside construction activities involves:
- Erection of steel or RCC columns/beams structural network for creating storage spaces of rectangular boxes. The vertical beams are erected first and then the cross horizontal beams are carried up to the walls forming 4–6 tiers. Wooden planks are placed over the horizontal beams, forming racks for holding the storage bags. In between the wooden planks, gaps are maintained for air circulation. Each rectangular box holds approx. 42 bags of 50 kg capacity.
- Thermal insulation of usually expanded polystyrene or mineral wool/glass wool slabs in 100 mm is fixed over the walls with wooden battens, vapour barriers (over the plastered brick surface) and finally plastered. The floor is insulated with expanded polystyrene slabs having concrete or stone slab finish. There is a false ceiling of rigid board, and insulation is placed over the false ceiling, with usually rice husk spread uniformly. Mineral wool/glass wool slabs stored in polythene bags are also used.
- Refrigeration system is usually hung on the top or the sides. The temperature desired for potato storage is 2–5°C.
- Usually, it is a single chamber with no partition walls in between.
- The staircase is usually at the centre in front of the door.
Of late, these conventional cold storages have become ineffective and inefficient mainly due to failure of the insulation and refrigeration system. The insulation wears away because of continuous moisture ingress through the plastered surface, leading to the surface becoming wet, loose and chipping off. This exposes the insulation and the wooden battens, which are then attacked by moisture that gradually destabilises the system and makes it ineffective. In cold storages, mice are very common and they destroy expanded polystyrene. In case of mineral wool, moisture gets trapped between the fibres, making them heavier and ineffective. The vapour barrier which is on the warmer side of the insulation and fixed over the plastered brick wall slowly and gradually gets exposed to the moisture ingress and gets dislodged from its place.
This results into the inner cold environment coming in direct contact with the outer brick wall. This situation leads to moisture deposition from the outer environment to the wall due to formation of cold spots. So finally, the insulation system is under attack both from the inside and outside. This makes the insulation wet, rendering it ineffective with the passage of time. One percent moisture ingress reduces insulation value by five percent. So at a point of time, insulation loses its resistance property and outside heat ingress increases. This leads to more running of refrigeration compressor and load on the refrigeration machinery, which in turn increases electricity consumption. With regular power cuts, the interior of the cold storage becomes warmer, leading to product deterioration. So it is a cyclic effect starting from construction methodology or system to improper running and finally attack on product storage life and losses.
Usually, most of the conventional cold stores have single, large chambers, so even when the storage is half filled, the entire refrigeration machinery has to be in operation, making the cold storage operating cost higher and making it a loss-making venture.
Insulation is meant to maintain a desired temperature for some time even when the refrigeration compressor is not functioning. It should not allow heat from the outside to penetrate through the walls and ceiling into the cold storage, thereby ensuring energy conservation. So, the slower the heat passage through the walls and ceiling, the slower would be the gain in temperature inside the cold storage when the compressor is not running. Consequently, in case of power failure, the inside temperature will remain congenial for a longer period of time. Otherwise, the moment the power goes off, the temperature will rise fast and the products inside will start to decay.
Insulation also helps in the running cycles of the compressor. The compressor can be switched off after reaching a lower or stable temperature and switched on when the temperature rises. The time gap between the “Off and On” function will depend on the efficiency of the insulation system.
In the present situation, almost all the old cold storages in India have faced or are facing inefficient insulation function, leading to refrigeration system failure. The insulation system was found to have lagged or deteriorated partially with the plaster or water soaked, making it ineffective. This leads to formation of cold spots on the walls. The continuous presence of moisture leads to algae formation, making the inside atmosphere filthy and leading to faster deterioration of products. So product decays, higher energy costs, and failure of the refrigeration system have led to many cold storages being closed down.
New insulation system
A thorough analysis was done of the existing cold storage problem in India, and it was found that the insulation system needs a complete revamp. The present insulation materials like expanded polystyrene and glass wool/mineral wool that are of open cell structure allow moisture ingress and deposition. The most appropriate modern insulation material for cold storage is a closed cell material like polyurethane foam. In Indian conditions, both in terms of techno-commercial factors and availability, polyurethane foam has much better insulation properties and higher thermal efficiency in comparison to the materials being used presently (expanded polystyrene/mineral wool/glass wool). Further, it has a density almost double that of expanded polystyrene. Because of its lower thermal conductivity value, the thickness required for polyurethane foam will be less, thus allowing more storing space inside. Moreover, PUF is not eaten by rats and insects. Another alternative is polyisocyanurate foam, which is an advanced fire safe insulation material. These two are also closed cell insulation materials with lower conductivity values and higher densities.
While selecting insulation for cold storage, one should differentiate it from an air-conditioned building. A building is a situation where the various occupants including human beings and electronic gadgets generate continuous heat. Further, there are windows and doors through which heat or cold comes in. So the design has to take care of all these aspects and has an effect on the insulation material and thickness, whereas in a cold storage the number of openings are limited and mostly closed and the products once stored will release humidity (whereas in an office building, human beings and electronic gadgets release only heat). Further, the product once cooled will act as a cold body emitting cold.
The problem with a conventional insulation system was not only the material but also the application procedure. Cold storage insulation is different from building insulation. In a normal insulation system, vapour barrier is applied on the warmer side of insulation. But in the case of cold stores, vapour pressure is from both sides, that is the outside environment as well as the inside of the storage while vapour barrier on the warmer side prevents vapour from the outside environment, and there is no system in place to stop the moisture ingress from inside. Since the inside cover or finish over the insulation is plaster, which is again a porous material, it will allow moisture deposition and absorption. So we need an insulation application where the insulation is covered with an impervious cover or membrane from both sides. This cover should be non-porous and mechanically stronger.
Another problem was the insulation form. Insulation is applied in slab form, allowing numerous joints to be properly covered with adhesive. Multiple layers with adhered joints have to be sealed properly, along with the vapour barrier. Presently, all these are highly labour-oriented and any lapse at any step will result into leakage and cold spot formation. Finally, while applying plaster, a reinforcement of wire netting is required above that has a high chance of puncturing the insulation. Plaster is porous and moisture from inside is gradually absorbed by it. So the moisture slowly kills the insulation system from inside.
Insulation thickness is an important tool for effective performance. If thickness is inadequate, there will be heat ingress continuously. In thickness calculation, humidity is an input. One should take care of considering the maximum RH happening in that area or remaining for sometime during the rainy season. Say, if average taken is 70 percent, then during the peak monsoon period when RH remains 85–90 percent, there will be cold spot formation. So it is advisable to factor in at least 85 percent during design.
Existing insulation system is highly labour-oriented, cumbersome and a basic drawback in terms of application methodology. Continuous supervision is required during construction.
Next comes the basic insulation material, which has a defined property with respect to the water/moisture ingress. An open cell structure material like a fibrous material or steamed, compressed, bead-filled insulation like expanded polystyrene will have the tendency to absorb moisture and retain it throughout. So once moisture enters the material, it will remain there, thereby reducing its efficiency. Ultimately, ice formation also takes place.
Now let us analyse which are the possible controllable factors. These are material, design, and procedure. Material can be changed to closed cell materials like polyurethane foam, polyisocyanurate foam, and extruded polystyrene foam. By opting for RH 85 percent, adequate thickness can be followed.
In terms of vapour barrier, the same can be applied on both sides. Insulation can be laminated on the facing side; similarly, vapour barrier can be applied on the wall. The first layer will be applied on top of a brick wall and then insulation laminated with aluminium foil on one side will act as a vapour barrier on the product storage side. Finally, colour-coated galvanised steel sheet (1 m wide and any length) must be fixed vertically or horizontally onto the supporting structure and the joints sealed with sealants and 75mm wide tape.
Repair of existing cold stores walls and roof insulation
The most efficient and latest technology application will be externally fixing of closed cell polyurethane foam insulation slabs with special water-based adhesive onto the walls and then applying polymerised plaster 4–6 mm thick in 2 layers, with synthetic reinforcement superimposed between both layers. The plaster after drying will have a natural finish (white colour). One can alternatively apply 2 coats of proper grade painting over the dried plaster. For the roof, polyurethane foam insulation shall be sprayed to form a uniform homogenous cover over the RCC roof, followed by plaster and suitable waterproofing treatment.
In this way, the wall and roof can be revamped.
Proper application procedure can be formulated, but the extent of control can only be determined during construction. The application procedure remains labour-intensive, requiring a lot of supervision and control. But it has to be seen how well the application is implemented. So changing or shifting to an efficient system is not the final solution — it is only a partial solution. The total construction time for a typical 5,000-tonne cold storage will remain to be around 9–10 months. So, if the harvesting time is February, construction needs to start by around May–June the previous year factoring in monsoon. So the basic system needs a correction.
For more details, visit:
http://lloydinsulations.com/
Email: kk.mitra@lloydinsulation.com
Cookie Consent
We use cookies to personalize your experience. By continuing to visit this website you agree to our Terms & Conditions, Privacy Policy and Cookie Policy.
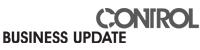