The goal of an optimised maintenance strategy is to develop a sustainable maintenance program for your chiller that helps extend asset life and reduce overall facility costs.
Chillers are a key component of an HVAC system. They extract the heat out of a building / HVAC system in the form of cold water. They also provide cooling for process loads like; server rooms, heavy medical imaging equipment among others. Since chillers are complex machines that are expensive to purchase and operate, a predictive maintenance manual and practice guide is catered for self help in best maintenance.
Inefficient chiller performance can also lead to decreased equipment reliability, increased maintenance intervals, and shortened lifespan. Even a slightest decrease in chillers performance can have a major impact on efficiency. For instance, every 1% F increase in condenser water temperature above full load design can decrease chillers efficiency by 1 per cent – 2 per cent. A failing or neglected water treatment program can reduce efficiency 10 percent to 35 percent or more in extreme cases.
Contrary to popular belief, running chillers at full load design and achieving the design kW/ton does not necessarily mean the chillers is running in its maximum efficiency. Maximum chillers efficiency is producing the greatest tonage at the lowest kilowatt usage. Maximum efficiency occurs with most chillers running at approximately 70-75 percent load and the lowest entering condenser water temperature (ECWT), based on design. Knowing a chillers’ efficiency and the effects of load and ECWT will help the facility determine the most efficient chillers configurations, saving the maximum on energy costs.
Document chiller data
To maximise your chiller’s efficiency, is imperative to establish a method to record chiller’s operational data in a daily log book. Maintaining chiller logs is a common activity in facilities but they are barely reviewed; this further leads to critical implications. The chiller operational logs can be easily maintained by entering the data in their daily logs through an efficient programme, like Efficiency Technologies Inc.’s Web-based Eff HVAC Chiller efficiency tool. HVAC is designed to accurately measure chiller performance at full and partial loads, calculate efficiency, and diagnose the causes of inefficiency. If past chiller logs exist, the data can be entered and a baseline can be immediately established.
Balancing temperature of chilled water and condenser’s water
Every 1 degree F increase in chill water temperature can boost chiller energy efficiency by 1 to 2 percent. For variable speed chillers, every 1 degree F increase in chill water temperature can result in a 2 to 4 percent efficiency increase. However, it may not be possible to increase the chill water temperature to save money due to design constraints, occupant comfort levels, or real-time energy pricing (sacrificing efficiency at one time to improve the efficiency at another time).
Take advantage of wet bulb conditions in the cooling tower system to lower the chiller’s entering condenser water temperature, this can improve the efficiency by 1 to 1.5 percent, for every 1 degree. It is important to note that part loads associated with chiller type (high or low pressure) and compressor motor style (constant or variable speed) will affect the chiller’s performance. Consult the chiller manufacturer to establish appropriate guidelines for entering condenser water temperature.
Best practices for efficient operation
Operate multiple chillers for peak efficiency: Plants with two or more chillers can save energy by matching the building loads to the most efficient combination of one or more chillers. In general, the most efficient chiller should be first one used.
Raise chilled-water temperature:
An increase in the temperature of the chilled water supplied to the building’s air handlers will improve its efficiency. Establish a chilled-water reset schedule. A reset schedule can typically adjust the chilled-water temperature as the outside-air temperature changes. On a centrifugal chiller, increasing the temperature of chilled water supply by 2-3°F will reduce chiller energy use 3-5 per cent.
Reduce condenser water temperature: Reducing the temperature of the water returning from the cooling tower to the chiller condenser by 2-3°F will reduce chiller energy use 2-3 per cent. The temperature set-point for the water leaving the cooling tower should be as low as the chiller manufacturer will allow for water entering the condenser.
Purge air from refrigerant:
Air trapped in the refrigerant loop increases pressure at the compressor discharge. This increases the work required from the compressor. Newer chillers have automatic air purgers that have run-time meters. Daily or weekly tracking of run time will show if a leak has developed that permits air to enter the system.
Optimise free cooling: A system having chiller bypass and heat exchanger, known as a water-side economiser, it should be used to serve process loads during the winter season. The water-side economiser produces chilled water without running the chiller. Condenser water circulates through the cooling tower to reject heat, and then goes to a heat exchanger (bypassing the chiller) where the water is cooled sufficiently to meet the cooling loads.
Maintain refrigerant level:
To maintain a chiller’s efficiency, check the refrigerant sight-glass and the superheat and sub cooling temperature readings, and compare them to the manufacturer’s requirements. Both low-level and high-level refrigerant conditions can be detected this way. Either condition reduces chiller capacity and efficiency.
Maintain a daily log:
Chiller O&M best practices begin with maintaining a daily log of temperatures, fluid levels, pressures, flow rates, and motor amperage. Taken together, these readings serve as a valuable baseline reference for operating the system and troubleshooting problems. Many newer chillers automatically save logs of these measurements in their on-board control system, which may be able to communicate directly with the DDC.
Maintain refrigerant levels
A chillers ability to efficiently remove heat directly correlates to the compressor’s ability to move the refrigerant per unit of time. It is important to maintain refrigerant levels as low levels cause the compressor to work harder and less efficiently. Check for leaks regularly, especially when a chiller shows signs of low refrigerant level. Trending refrigerant levels will help determine if the chiller has a leak, a bad purge unit, or refrigerant carryover.
Refrigerant analysis:
Regular refrigerant analysis is an important part of determining chiller inefficiencies. If oil content in the refrigerant is above the chiller manufacturer’s guidelines, it may be reducing heat transfer. Keeping good maintenance records on oil usage in a chiller will help to avoid this condition.
Preventive maintenance
Compressor oil must be analysed annually. Low-pressure chillers may require frequent analysis depending on the based on purge run hours. This test should include a spectrometric chemical analysis containing information on metals, moisture content, acids, and other contaminants that can alter the chiller performance. Replacing oil filters whenever on high pressure drop or when the compressor oil is changed. Consult your chiller manufacturer, lubricant supplier, and/or oil analysis laboratory for oil and filter change intervals.
Cookie Consent
We use cookies to personalize your experience. By continuing to visit this website you agree to our Terms & Conditions, Privacy Policy and Cookie Policy.
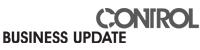