Refrigeration is increasingly becoming one of the driving forces behind smooth operations of essential industries around the world and the adoption of process chillers in industrial settings. The sector of industrial refrigeration comprises a vast range of processes including chilling and low temperature freezers. Its widespread applications have made it a large scale sector.
With increasing emphasis being on efficiency and faster delivery, the importance of industrial process chillers in end use industries such as construction, manufacturing, and food cannot be understated. Industrial process chillers are essential for maintaining operational temperatures for specific industrial tools and equipment. Failure of such chillers can put the entire refrigeration process at risk, while operations are key to optimal running of processes.
Industrial process chillers manufacturers have to keep essential factors such as costs, complexity of installation efforts and networks as their focus in order to maintain operations in such a specialised field. In addition, tech innovations have largely divided process chillers into water cooled and air cooled process chillers variants.
Factors to consider while adopting industrial process chillers
Industrial refrigeration operations are playing a key role in a wide variety of end use industries including construction, food processing, manufacturing, chemicals, and pharmaceuticals. Most of these users prefer the use of water cooled chillers, which require a large amount of water for regular operations. Industrial process chillers can come in a number of configurations, with capacities ranging from one ton units to thousand ton options.
In addition, water cooled chillers are designed to be installed indoors. While such portable industrial chillers are considered to be more efficient, and also have a longer life, water cooled industrial process chillers are normally more expensive owing to higher maintenance costs.
Of the different end industries, food processing is a major buyer of industrial process chillers, with key roles in the running of businesses such as bakeries, wineries, and dairies needing requisite cooling equipment.
For instance the cheese and wine industries require industrial water chillers, which is the key for not only the multi stage production processes, but also for maintaining the longevity of other equipment being used.
Manufacturing plants are the major contributors to the demand for industrial process chillers, as highly accurate cooling processes are needed for extreme condition testing in different environments, including high and low temperatures, and variable humidity conditions needed in handling metals and plastics.
Further chillers in pharmacy and chemical industries require industrial process chillers to meet specific regulatory parameters, owing to high accuracy processes of humidity control, and gas condensation, which drives the demand for versatile refrigeration plants. Similarly, the construction industry needs industrial process chillers for activities such as hardening concrete, freezing wet soil, and preservation in excavations.
Modern industrial process chillers gain traction to meet wider refrigeration demands
As industrial applications advance faster, modern industrial process chillers are needed to run for longer periods, consuming more resources to keep up with the requisite performance improvements. With changes in the industry, manufacturers are being pushed to develop chillers with lower temperature capabilities, which generate higher quantities of insulation.
Other chillers are being designed to run with multi stage cooling operations, which will require more evaporators and compressors. With such demands coming out of end use industries, industrial cooling chillers are increasingly being complemented with additional equipment such as low pressure receivers to separate liquids from vapour, and in some cases suction traps, which restrict liquid refrigerants from entering compressors.
Breakthroughs in cost control and energy efficiency
Newer lines of industrial process chillers have been displaying massive improvements in terms of accuracy in temperature control, while also needing only half the energy of conventional devices. Newer chillers are coming out with features which are either new to the field, or which have not been used across the board in differing configurations.
Major manufacturers are pushing for the development of smaller, portable, air cooled chillers reaching up to 30 tons in capacity. While most of these portable industrial process chillers are expected to be initially designed on the air cooled working principle, water cooled variants are also expected to be introduced in the near future.
A recent innovation in this direction is the use of compressor technologies that can operate on variable speeds. Earlier, such technology was restricted solely to HVAC equipment, and is for the first time being used in process chilling applications.
Such technologies monitor the real time process temperatures, and accordingly transmit signals to the compressors to either speed up or slow down. Such equipment will not only benefit from lower wear and tear, by the elimination of cycling in compressors, but will also result in reductions of up to 50 per cent in energy requirements, which will help in recovering much of the initial investments made in such equipment.
Conventional chillers are designed only to meet the demand for peak season operations, which means, such industrial process chillers are too large for pragmatic usage. Consequently, the smaller, portable industrial process chillers with newer, efficient tech is more likely to gain higher rates of sales.
Additional energy and monetary savings are also made possible through the adoption of variable speed, hydraulic pump drives; which is often integrated with hot-gas bypass valves that pushes hot gases to evaporators, in cases where cooling loads become unnecessary. In addition, such changes also allow newer industrial process chillers to handle loads between 1 and 10 tons at the same level of efficiency.
Other technologies that are expected to have a bright future in the industrial process chillers sector include variable speed condenser fans with real time monitoring capabilities and electronic expansion valves, which can supplement variable speed compressors to adjust the valve to operational requirements based on pressure and temperature sensors.
Further, the advent of industrial internet of things and big data tools are going to gain a larger footprint with the introduction of multiple sensors to study factors such as alarms, pressure, temperature, fan outputs, and phase monitoring readings among others, which will sustain demand for small process chillers in the foreseeable future.
This report is posted on FACT: MR website, we would like to appreciate the research on the subject. There are minor changes in the report as to make it up-to our editorial style.
Cookie Consent
We use cookies to personalize your experience. By continuing to visit this website you agree to our Terms & Conditions, Privacy Policy and Cookie Policy.
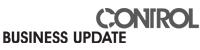