To prevent corrosion in chilled water systems and ensure smooth processes, plant operators should check the water conditions regularly. They may then need to take measures dealing with, among other things, the pH value, hardness and conductivity of the water.
These days, reliable cooling is indispensable for many technical applications. This is true for process and industrial cooling, medical technology and – above all – server rooms and data centres. When it comes to the air conditioning of IT equipment, in particular, even minimal disturbances in the cooling system can incur expensive consequences. Therefore, for many years the IT sector has made use of defined availability classes and systems with in-built redundancy to reduce the risk of failure.
Besides planning and structural measures, any availability concept should also include a permanent maintenance and service strategy. Leak checks, regular filter replacement and the cleaning of heat exchanger surfaces should all take place as a matter of course. But in addition, continuous monitoring of the water parameters is a vital part of preventive corrosion protection.
The fact is that plant operators who continually keep an eye on water quality – right from the time the system is first filled – improve the general service life of their system and reap the benefits of constantly higher efficiency. Rule 3.003 from the BTGA (German Association of Technical Building Equipment) describes the correct procedure for producing and maintaining ideal water quality. It provides clear specifications on water-borne constituents and, furthermore, on how system maintenance, filling and monitoring should be carried out.
The type of chilling system is also an important factor here. Two different system designs generally predominate in the field of data centre cooling: precision air conditioning units with integrated DX refrigerant circuit and CW indoor units that are connected via heat exchangers to a central chiller.
In both models, the water circuit must be kept free from foreign matter and sediment and rich in oxygen to ensure a long service life and unrestricted function. Current research projects show that closed circuits in chilled water and liquid cooling systems can suffer their first corrosion damage within just one or two years. This is a problem not just because of damaged pipes and eventual leakage, but also because flaked off particles of corrosion can easily clog pumps, filters, and the capillary tubes of heat exchangers.
Four main types of corrosion
Oxygen corrosion is caused solely by dissolved oxygen in the water. It disappears over time in closed systems, but a residual content of oxygen must be reckoned with. If oxygen, water and metal (mostly iron) react with one another, the metal will suffer oxidation or corrosion.
With hydrogen or acid corrosion, an excessively low pH value (<5 pH) causes acid to attack the metal, corroding it or splitting it into ions, ultimately forming elementary hydrogen. This reaction can take place without oxygen, and the more acidic the environment, the faster and more aggressive the process.
Electrochemical corrosion is also referred to as galvanic corrosion. For this to happen, two dissimilar metals with different positions in the electrochemical series must be in contact with one another. The less noble metal releases electrons and oxidises. The result is the constant degradation of the material. The further apart the metals in the electrochemical series, the faster and more aggressive the corrosion process. Water and the minerals it contains act as a conductive medium.
Bacterial corrosion can also occur without oxygen. Bacteria draw electrons out of the metal, causing it to oxidise. Sulphur oxide is produced as a waste product of the bacteria, which provokes a strong odour in the surrounding fluid and can be an indicator of a bacteriological load.
Water quality matters
Most water circuits make use of a variety of materials, with very different chemical properties. The most common of these are black steel, copper, stainless steel, grey cast iron, aluminium, silver solder, and rubber seals. In most cases, advance corrosion prevention through design – by using harmonised materials, for instance – is extremely expensive and unfeasible. Therefore, the question is how to best protect the system against corrosion. Often, the only sensible and also easiest method of corrosion protection in chilled water systems is simply to keep checking and adjusting the water conditions.
The quality of the water in the circuit is fundamental, as this is what makes the risk of corrosion damage rise or fall. However, water quality must not be assessed on the basis of a single parameter; rather, its composition is interpreted entirely differently depending on the intended purpose and the given conditions. Indeed, the corrosively of a particular water mixture is not classed identically for every material and cooling circuit. Rather, the oxygen content has a major influence on corrosion. If there is a large proportion of oxygen, a higher degree of corrosion can be expected. The oxygen dissipates rapidly in closed systems, however. Oxygen can also be chemically bound in order to prevent oxygen corrosion. But there are other important factors determining the corrosively of the water in a circuit, including the water’s pH value, hardness and conductivity.
The pH value is the measure of an acidic or base aqueous solution. Tap water has an average pH value of 7.5. Both an overly high and an overly low pH value should be avoided. Different materials have different pH value ranges, within which they are able to form a protective oxide layer. If an installed material is above or below this range, the risk of corrosion increases dramatically, leading to acid corrosion as mentioned above. The difficulty with pH values is that after a system has been filled, the water in the circuit still contains a high proportion of dissolved carbonic acid. This gradually escapes as carbon dioxide – but then the lack of carbonic acid causes the pH value to rise. Therefore, it is almost impossible to adjust the pH value precisely. If the pipe network contains a mix of materials, this considerably narrows the range within which the pH value will not provoke corrosion in the components. This is clearly illustrated in the diagram below.
The hardness of the water is determined by its content of alkaline earth metal ions. There is carbonate hardness – also referred to as temporary hardness – on the one hand. This is chiefly caused by cations of magnesium and calcium. On the other hand, there is also an element of permanent hardness, which cannot precipitate as an insoluble solid. In warm parts of the circuit, the non-permanent hydrogen carbonates, which are dissolved in the water when a circuit is filled, precipitate as carbon dioxide and carbonates. The result of this combination is commonly also referred to as “limescale”. This substance adheres to the inside of heat exchangers and pipes, leading to huge losses of efficiency in the entire system.
The conductivity of the water is determined by the quantity of dissolved anions and cations it contains. These include hardness builders such as magnesium, calcium and hydrogen carbonate, but also minerals and dissolved metal ions. The more particles the water contains, the higher it’s conductivity and therefore its susceptibility to electrolytic corrosion. Moreover, this increases the likelihood of sediments in the water. The best known exponent of this is lime scale, which always forms at the warmest point with the slowest flow in a chilled water system, which in most cases is the heat exchanger. There is now an acute risk of heat exchanger clogging, which has a hugely negative impact on efficiency. This is because of the smaller contact surface and the fact that lime scale has a far lower thermal conductivity coefficient than copper. Partial lime scale deposits can also cause stress cracks in the heat exchanger due to the varying heat expansion. High conductivity does not necessarily constitute a higher risk, however. Corrosion inhibitors increase conductivity, for example, but in this case it is not problematic.
When checking the water conditions, particular attention should be paid to minerals. Dissolved minerals are especially critical for the refrigerant circuit, because they are highly reactive and provoke both precipitation and corrosion. Chloride is the salt produced by hydrochloric acid and is the most stable parameter in the circulatory system. It is primarily used as a chemical catalyst, but it also intensifies corrosive processes. During this acceleration, chloride is not used up, but is retained. In addition, chloride attacks the passive layers on metals, exposing more surfaces to attack from normal oxygen corrosion. In certain conditions, chloride can cause local damage that result in pitting corrosion.
Sulphate is the salt produced by sulphuric acid and acts as a nutritional basis for any bacteria in the circulatory system. These are then silicate-reducing bacteria. The combination of calcium and oxidising to form calcium sulphate can also be an indicator of sulphate reduction. Generally, these very hard deposits are responsible for poor temperature transitions and inefficient operation.
Bacterial processes cause nitrate to transform into ammonia and to react with copper pipes to form a copper ammonia complex, which is capable of oxidising iron without a supply of oxygen while disintegrating back into ammonia and copper. Through the process of complexing, ammonia therefore continually oxidises the iron constituents of a circuit. Tap water has a relatively low nitrate value, and in technical use can be regarded as critical from approx. 5 mg/l. However, the nitrate level is becoming increasingly relevant in the evaluation of corrosion risks, due to the rising concentration of nitrate in the groundwater, particularly in agricultural areas.
Risk due to added glycol
Depending on their installation location, water circuits are often filled with a water-glycol mixture to prevent the pipe work from freezing. However, in certain circumstances glycol can intensify the corrosive properties of the water. With a neutral pH value and a low-oxygen environment, corrosively scarcely differs from pure water. But if oxygen is dissolved in the water, glycol can break down. This produces acids that acidify the water-glycol mixture, lowering the pH value. Acidification of the mixture can lead to pH values of less than 4. Consequently, as well as the usual corrosion inhibitors, antifreeze concentrates also contain acid neutralisers, which can mitigate the acidification to a certain extent. There are only a limited number of these acidic buffers in the mixture, however, which is why both the pH value and the glycol content of the circuit need to be checked. Furthermore, if the glycol concentration falls below the minimum value specified by the manufacturer, increased bacterial growth can be expected. This results in organic deposits and bacterial corrosion. Common minimum levels are 20 percent by volume for ethylene glycol and 25 percent by volume for propylene glycol. Here, it may be a good idea to contact the glycol manufacturer or to read the manufacturer’s technical data sheets.
Conclusion
Basically, the oxygen content should be kept to a minimum and the system kept free from leakage. Chlorides and sulphites must be reduced in line with the Rule 3.003 from the BTGA, and the use of water with a low mineral content is also recommended. In addition, it is important to keep the pH value within the middle range, to suit the resistance of the materials used, and to check this regularly. Softeners and residual hardness stabilisers are also recommended. The use of demineralised water is disadvantageous as it is acidifying and highly reactive. If pure water is used, the lowest possible conductivity should be aimed for, as well as a nitrate content of less than 5 mg/l. The use of corrosion inhibitors or glycol mixtures in the right concentration is also advisable, as is constant monitoring. Despite the fact that Rule 3.003 from the BTGA is not a standard, but a technical rule, it is extremely pertinent in this field. If plant operators ensure that the system is low in minerals right from the start, in accordance with this Rule, and take care of the water conditions, they can increase the efficiency and service life of their chilled water systems.
(This case study has been authored by Tobias Wolf, Deputy Head of Product Management STULZ)
Cookie Consent
We use cookies to personalize your experience. By continuing to visit this website you agree to our Terms & Conditions, Privacy Policy and Cookie Policy.
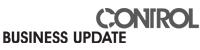