An upgrade required heat exchangers to raise the temperature of the product from -5°C to 18°C before the final heater, which includes melting the frozen product.
Burra Foods, a prominent player in the Australian dairy industry, specialises in producing value-added dairy products for the global food manufacturing market. They recently embarked on a plant upgrade in Korumburra, Victoria, to improve their dairy processing capabilities.
The challenge
Its quest to enhance its dairy production faced a unique challenge. This necessitated using a heat exchanger to help produce skimmed milk concentrate and cream from frozen concentrates, which are then thermalised and cooled to ambient processing temperatures. The process required elevating the product’s temperature from -5°C to 18°C before it could undergo further heating and cooling stages. After this, the product is cooled from 10°C to 5°C in the final cooler. This included the critical task of melting the frozen product. The key challenge was the product’s viscous consistency, which tended to cause fouling in conventional heat exchangers. Additionally, the available space for installation was severely limited due to existing building and infrastructure constraints.
The solution
Burra Foods found a suitable solution in the HRS MI Series corrugated tube heat exchanger. This innovative heat exchanger met the stringent heating and cooling requirements and proved to be a space-efficient choice. The corrugated tube design enabled efficient heat transfer while resisting fouling, making it an ideal fit for the challenging dairy processing environment. Importantly, the HRS heat exchanger delivered excellent performance with a small pressure drop, a crucial consideration for this installation.
The HRS MI Series heat exchanger was installed and has consistently exceeded performance expectations since its commissioning. It enables a remarkable production capacity of 5,000 kg of dairy product per hour, showcasing its efficiency and reliability.
Feedback and flexibility
Stuart Shattock, the Process Engineering Manager at Burra Foods, expressed their satisfaction with the solution provided by HRS. He noted that other suppliers could not match HRS’s offering, particularly in tubular heat exchangers and the level of detail provided during the consultation and procurement process.
Despite the challenging circumstances posed by the COVID-19 pandemic, HRS managed to produce it as a rush order, and the installation and commissioning were smooth. There was a slight delay in production due to the pandemic, but HRS responded by treating the project as a rush order, demonstrating their commitment to meeting their client’s requirements. Stuart Shattock commended HRS for their flexibility and adaptability during the installation phase. He highlighted that the HRS team was accommodating and capable of making real-time process design improvements during installation, contributing to a smooth and successful project outcome.
Conclusion
The collaboration between Burra Foods and HRS exemplifies how innovative engineering solutions can overcome challenging operational constraints in the food and beverage industry. The HRS MI Series corrugated tube heat exchanger has proven to be a pivotal component in Burra Foods’ upgraded dairy processing plant, enhancing efficiency and production capacity while maintaining the highest product quality standards. This case study underscores the importance of finding the right partner to provide tailored solutions and adapt to evolving project requirements, especially in food and beverage processing industries.
Source: www.hrs-heatexchangers.com
Cookie Consent
We use cookies to personalize your experience. By continuing to visit this website you agree to our Terms & Conditions, Privacy Policy and Cookie Policy.
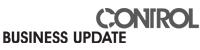