Unleashing the Power of Technology to revolutionise India’s cold chain industry, cold chain professionals share their views on potential opportunities for improving logistics development, boosting capacity, cooling technologies, innovative equipment, and growth prospects of automation in the cold chain.
The global cold chain market experienced a valuation of USD 279.94 billion in 2022, and it is projected to exhibit a compound annual growth rate (CAGR) of 18.6% from 2023 to 2030. The industry’s expansion in the coming years will be driven by factors such as the widespread adoption of connected devices and the automation of refrigerated warehouses worldwide. The emergence of organised retail stores in developing nations also contributes to the rising demand for cold chain solutions. Additionally, governmental initiatives to minimise food waste, trade liberalisation efforts, and the expansion of multinational retail chains are expected to stimulate this industry’s growth further.
Mr. Swarup Bose, Founder and CEO, Celcius stated, “In 2021, it was found that approximately 80% of cold chain warehouses in India lacked automation, including proper warehouse management systems (WMS). Although WMS usage has started to increase, it is not as widespread as desired, especially compared to the global industry worth around $900 billion. However, it is projected that by 2027, over 70% of warehouse operations worldwide will be automated, with robotics playing a significant role in tasks like product placement and e-commerce logistics. The extent to which India will catch up with this trend by 2027 remains to be seen, but the future lies in automation. With the rise of e-commerce players like Zeptto, Zomato, and Swiggy entering the cold storage sector and the gradual adoption of advanced technologies prevalent worldwide, India is making progress, albeit at a slower pace. Overall, this indicates a positive trajectory towards embracing automation.”
Technology adoption in the warehouse sector
Mr. Parth Thakkar, Director, Polfrost Aircon Pvt Ltd said, “In India, the implementation of AI, digital transformation, and WMS technologies in warehouses is still preliminary. While the necessary technologies and knowledge are available, there is a need for mindset change and improved education among equipment operators. Lack of proper skills can lead to challenges and failures in utilising advanced technologies. Organised market players have access to WMS and ASRS technologies, while most of the country’s warehouses remain unorganised. This knowledge gap hinders widespread adoption and leaves many individuals without the necessary expertise. Progressing in advanced technologies requires starting with the basics and obtaining crucial data for training models. Mr. Rajat Gupta, Co-founder and CEO, TESSOL, added, “Although there is still a long way to go, we have shown a remarkable ability to adapt quickly once we have access to the right technologies. We embrace change and have swiftly adopted temperature monitoring and data sharing in field deployments. Implementation is not a major challenge, but higher-level decision-making remains crucial. Overall, there is a positive acceptance and willingness to adopt technology in the country.”
Infrastructure Challenges
Due to subsidy applications, cold chain warehouses built in India typically adhere to standardised rules and guidelines. The infrastructure itself is not the issue; the challenge lies in shifting mindsets towards accommodating multi-commodity storage and enabling collaboration with e-commerce platforms. The rise of e-commerce in India requires a different mindset than traditional warehousing, which involves continuous movement of goods rather than bulk storage for specific dates. According to Mr. Swarup, labor training plays a crucial role, with warehouse operators responsible for managing operations and ensuring workers adapt to new systems introduced by e-commerce platforms. This includes implementing inventory management systems and having competent supervisors and staff capable of adjusting to these changes.
The current infrastructure of warehouses needs modification to address specific issues. For instance, anti-chambers in warehouses are typically not temperature controlled, but they serve as transitional areas. In India, where ambient temperatures can reach 45- 50 degrees Celsius, even a brief 10-minute placement of frozen materials in such non-controlled areas can result in temperature loss, causing melting or softening. This negatively impacts the end-user experience. Warehouse operators must understand the importance of creating proper temperature controlled anti-chambers and ensuring dock areas have suitable buffers to prevent product temperature breakage. From the moment of acceptance to storage, maintaining proper temperature conditions is essential. Currently, it is unlikely for the Indian economy to embrace automation with robotics due to cost constraints. However, there is potential for this attitude to change in the future. In the meantime, efforts can be focused on improving daily transactions and ensuring professional handling of incoming products by leveraging technology and adapting to it.
Enhancing energy efficiency in Cold Warehouses
Mr. Vishnu Sasidharan, VP, Climate Technologies, Pluss Advanced Technologies, elaborated that as a provider of phase change material-based solutions for thermal management, their primary objective is to enhance energy efficiency and promote decarbonisation. They recognise several opportunities in this pursuit, including the need for better visibility into energy consumption and identifying inefficiencies. While monitoring temperature and electricity usage is essential, other parameters, such as tracking the frequency of opening and closing cold warehouses to assess operational efficiency, are worth considering. However, when engaging with end users and operators, they have observed insufficient insights regarding the sources of inefficiencies. Often, the available data could be more accurate or conclusive, hindering effective decision-making. While high-tech solutions may not be necessary, there is an increasing awareness of the importance of energy efficiency. Customers are willing to invest in technologies that can demonstrate improved efficiency, leading to the emergence of cooling-as-a-service models. However, the challenge lies in assessing the current energy situation and providing proof of efficiency gains before implementing new technologies. Many cold warehouses need the basic infrastructure for measurement, making it easier to evaluate the existing conditions. Therefore, conducting a thorough initial study is essential, as even minor operational adjustments can yield significant efficiency improvements without relying heavily on technology.
Refrigerant solutions
The solution to any problem depends on the specific requirements at hand. For instance, passive cold boxes and cool containers can be considered for short-haul and smaller transportation needs. On the other hand, for longer distance movements involving larger trucks, eutectic-based solutions are more suitable, especially for distribution applications within a 24-hour timeframe. “Conventional solutions have proven efficient for scenarios involving full-load trucks spanning 20-32 feet. Users must understand that there is no one-size fits-all solution. Optimisation depends on identifying the application and selecting the appropriate technology accordingly, rather than adopting a single technology for all scenarios,” said Mr Rajat. Mr Vishnu elaborated that complete isolation of refrigerants has yet to be achieved, but there is a need to generate energy for storage purposes. Like lithium-ion batteries are essential for electric vehicles, PCM (Phase Change Material) plays a crucial role in thermal management. Storage offers flexibility in the supply chain, and significant progress has been made in the past decade. Various industry players and companies provide solutions beyond traditional ice packs, enabling the transportation of frozen products with innovative methods. Circular approaches and thermal energy storage contribute to optimising operations and reducing dependence on fossil fuels while promoting the use of renewable energy. Although refrigerant-based cooling units still rely on refrigerants, their usage can be minimised using storage mediums. A combination of energy storage and direct energy usage offers opportunities for optimisation. It can be compared to using a laptop, where you can either keep it plugged in for continuous power or unplug it for mobility and plug it back in when needed. These solutions provide flexibility based on user needs. For example, if you require mobility, you would use more storage to support intermittent use. Previously, such options were not available, limiting optimisation possibilities. Technology has opened up new avenues beyond traditional optimisation strategies focused on cost reduction and shortcuts. Users can now optimise their systems according to specific applications. While newer technologies offer benefits, traditional approaches still have their place and are unlikely to become obsolete. Ultimately, users determine which approach is best for their requirements.
Initiatives to induce growth in the warehousing automation industry
Regarding government support for the warehousing industry, subsidies are the most effective way to encourage the growth and adoption of new technologies. Since cost reduction is crucial in the cold chain sector, subsidies can make a significant impact in making operations more seamless and affordable. The government’s assistance enables the industry to reduce costs and make necessary advancements. According to Mr. Parth, various measures can be implemented to incentivise the private sector’s adoption of new technologies and green initiatives. The private sector has already demonstrated its commitment to such initiatives and has received support from financial institutions.
Transitioning from cost reduction to cost optimisation
The cold chain industry is currently burdened with high costs, which cannot be passed on to end customers. This creates constant pressure to lower prices throughout the entire ecosystem. However, shifting focus from merely reducing costs to optimising them is essential. Automation, IoT, and green technologies have a significant role in achieving this optimisation. The industry experiences wastage, overdesign, and excessive expenses due to breakdowns, all of which can be mitigated by embracing advanced technologies. While the government can assist in cost reduction, the private sector, along with the support of banks, holds the potential to drive the adoption of greener infrastructure and prioritise energy optimisation. Mr Swarup stated that the government is actively promoting digital transformation, as seen in the digitisation of logistics and e-commerce sectors. Their efforts to digitise the warehousing supply chain have a significant impact, particularly in tier two and tier three cities, where technology adoption is faster and facilitated by government initiatives. While our platform remains accessible for free, adopting other costly technologies poses challenges for businesses struggling to generate profits. In such cases, government intervention becomes crucial. Banks have also recognised the value of technology, such as WMS and inventory management systems, and use them to assess risk and offer better interest rates to smaller storage facilities. This recognition of improved efficiency through technology encourages businesses to embrace these systems. Overall, with the collaboration of these various processes, we can expect greater future benefits.
It is widely acknowledged that the importance of technology exists, but the constraints and challenges are apparent. Therefore, finding a middle ground through innovative business models that can address initial financial impacts while introducing technology and creating mutually beneficial business propositions is necessary.
“While the necessary technologies and knowledge are available, there is a need for mindset change and improved education among equipment operators.”
Mr. Parth Thakkar, Director, Polfrost Aircon Pvt Ltd
“Circular approaches and thermal energy storage contribute to optimising operations and reducing dependence on fossil fuels while promoting the use of renewable energy.”
Mr. Vishnu Sasidharan, VP, Climate Technologies, Pluss Advanced Technologies
“Optimisation depends on identifying the application and selecting the appropriate technology accordingly, rather than adopting a single technology for all scenarios.”
Mr. Rajat Gupta, Co-founder and CEO, TESSOL
“Labor training plays a crucial role, with warehouse operators responsible for managing operations and ensuring workers adapt to new systems introduced by e-commerce platforms.”
Mr. Swarup Bose, Founder and CEO, Celcius
“Instead of creating separate cold rooms within the warehouse, construct the entire warehouse to minimise the need for refrigeration.”
Mr. Vikas Choudaha, Senior Vice President & Business Head, Godrej Storage Solutions, Godrej & Boyce Mfg. Co. Ltd.
“Consumers these days seek quality and hygienic products which constitutes a constant responsibility to increase the shelf life of the products for consumption.”
Mr. Sushil Teotia, AVP, Bry-Air.
Cookie Consent
We use cookies to personalize your experience. By continuing to visit this website you agree to our Terms & Conditions, Privacy Policy and Cookie Policy.
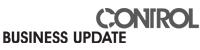