The best thing about technology is, it is ever evolving, revealing new innovations and opportunities. And as these new technologies come to light, heat treating operations have new opportunities to reduce cost, increase efficiency, and ensure consistent, optimised part quality, regardless of the job parameters. With the introduction of new process cooling technologies to the heat-treating market, previously unexplored systems become viable solutions for unanswered operating challenges.
When a tempered alloy manufacturer faced strict job requirements that demanded capabilities outside the competences of traditional technologies, a modular process cooling systems designer and manufacturer based in Italy with a North American operation located in East Dundee, Illinois, proposed a process cooling system that addressed key problem areas, while ensuring top system performance. As a result, the company was able to document operational cost savings of over $80,000 per year.
Initial investigations into solutions revealed apparent limitations. Traditional process cooling methods were unable to cost-effectively maintain water-cooling temperatures of 70°F. This made finding an alternative solution critical. Three traditional methods were explored:
Evaporative cooling towers
This technology is incapable of achieving consistent temperatures in the 70°F range. Cooling water temperatures are controlled by the wet-bulb temperature, relying on evaporation in ambient air conditions. As a result, they can often only provide 85°F or higher water temperatures to processes year-round. This cooling technology tends to be maintenance-intensive given the reliance on chemical treatment and filtration to maintain water quality. Additionally, evaporative towers consume excessive amounts of water.
Dry fluid coolers
This technology would only be effective in this application when air temperatures were at 55°F or below. Though reducing the need for chemical treatments and eliminating excessive water consumption, this system can only produce water that is typically 10-15 degrees warmer than the dry-bulb temperature, or the ambient air temperature without moisture. As a result, temperature tolerance would be lost during the warmer months. During the colder months, the use of glycol antifreeze solutions is necessary to maintain system functionality, which in many cases requires the use of additional pumping systems and water-to-glycol heat exchangers.
Central chillers
The conventional approach relies on a chilled water system that incorporates chillers to generate 70°F temperatures. This system can be supplemented with a dry fluid cooler if conditions for free cooling were significant enough for payback in three years or less. In many cases, the cold, consistent temperature of the water produced by the chillers is cooler than is necessary for most heattreating components, leading to increased energy inefficiencies and accrued higher costs.
Faced with the limitations of traditional technologies, the manufacturer turned to an alternative process cooling system for the answer.
Considering an alternative system
Once traditional methods were thoroughly analysed, the choice was easy. Providing an alternative solution, the Frigel system design was selected and implemented into the vacuum furnace cooling application.
Frigel’s Intelligent Process Cooling systems are designed to create better processes for heat treating operations and provide a unique, flexible solution. The solution combines the use of its internationally patented closed-loop adiabatic fluid cooler with small, dedicated chillers to maximise opportunities for free cooling while ensuring consistent and reliable process cooling temperatures. The closed-loop adiabatic fluid cooler operates outside of the facility, with chillers located near each work cell or process. This approach allows for greater flexibility as individual process cooling needs change.
As a closed-loop system, it requires fewer resources and creates additional opportunities for free cooling capabilities. Water consumption is greatly reduced as opportunities for evaporation are removed. Water consumption is lowered by as much as 95 percent when compared to an evaporative cooling tower. The closed-loop system also prevents process cooling water from being exposed to the outside air, reducing the need for chemical treatments and additional filtration efforts.
For more details, visit:
www.frigel.com
Cookie Consent
We use cookies to personalize your experience. By continuing to visit this website you agree to our Terms & Conditions, Privacy Policy and Cookie Policy.
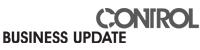