Mayfran is the world’s leading specialist in the handling of swarf and cooling lubricants during machine tool operations. Many customers particularly acknowledge the broad range of expertise in matters relating to the high-pressure supply of cooling lubricants in deep-hole drilling.
With more than 1,000 employees and manufacturing sites in the USA, Europe, Japan, Korea, India and China, Mayfran is the world’s leading producer of conveyor and filter plants for the metal processing industry.
E-Solution increases process efficiency and reduces energy costs Today, even standard CNC processing machines are available with high-pressure inner cooling so that they can be used for deep-hole drilling with an internal cooling lubricant feed and external swarf recovery.
In standard operation, the highpressure pump used to supply the cooling lubricant is driven by a motor with a fixed speed and thus constant volume flow. This volume flow is conveyed regardless of the quantity of cooling lubricant the machine tool or tool actually needs for the required pressure. In addition to wasting energy, this mode of operation also has further undesirable side effects for the deep-hole drilling process – for example, unnecessary heating of the cooling lubricant and increased foam production.
Detail of the Vari-Flow technology, including MTSE pump, integrated into a Mayfran filter system.
The benefits of automatic pressuredependent volume flow adjustment at a glance
- Higher process security through reduced tool wear and better surface quality (drill quality): the online control loop ensures that the required cooling lubricant pressure is actually present at the drill edge.
- More flexible process adjustment to multiple tools in the case of machine tools with automatic tool change or several machining operations occurring in parallel: after a tool change or the connection of a further machining process, the exact volume flow required for the new tools will be supplied automatically.
- More precise process controls: the comparison of the target/actual values of the cooling lubricant pressure can be used for a feed rate enable of the screw, thereby preventing tool breakage. The wear status of the high-pressure pump can also be recognised in good time through the speed control.
- Energy savings and reduction in size of the peripheral components: the use of Vari-Flow technology reduces operating costs by up to 75 percent – both through energy savings and the optimisation of the machining process using automatic data storage and programmed analysis. In addition, when using online high-pressure control, in most cases the design engineer can draw on smaller components (e.g. a smaller high-pressure pump, smaller cooling lubricant coolers and containers).
The new Vari-Flow technology is available for the entire HPM product range (‘High Pressure Machining Systems’) from Mayfran. HPM high pressure systems are offered as extension modules for filter systems, as stand-alone booster units, including a filter unit, and as a mobile auxiliary device with or without autonomous control.
The solution
In 2006, Mayfran launched a project, together with Grundfos, with the aim of developing a new technology platform for high-pressure cooling lubricant supply that eliminates the aforementioned disadvantages of an unregulated cooling lubricant pump. This process control, called ‘Vari-Flow’, is based on the Mayfran HPC controller and Grundfos E-Solutions technology, implemented using an MTSE screw pump with a speed-controlled MGE motor.
This three-spindel, self-priming screw pump has an impressively high delivery pressure of max. 130 bar. It is highly efficient and, as a result of the design, is particularly quiet in operation. This highly wear-resistant system also guarantees a high level of reliability and minimal vibrations.
“The company benefits from lower energy costs, a higher level of process security and high process quality” (Dipl. ing. René Sieben, Construction Manager, Mayfran GmbH, Aachen).
The outcome
The innovative Vari-Flow online highpressure process control system, based on the MTSE screw pump, adjusts automatically to the pressure/volume flow requirements of different drills.
The major advantage for the operator is that with this combined E-Solution (Mayfran: HPC controller/ Grundfos: GENIbus & MTSE), the operator has access to an adaptive system that responds to process conditions and actively adjusts to achieve an ideal state. The operator benefits from lower energy costs, greater process security and high process quality. In addition, saving process data creates a ‘transparent’ process; based on the available data history, the operator can further optimise the machining process, thereby reducing costs.
Cookie Consent
We use cookies to personalize your experience. By continuing to visit this website you agree to our Terms & Conditions, Privacy Policy and Cookie Policy.
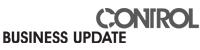